how many actually "tin" your wire before.....
#1
Thread Starter
tom port.. AKA streetport
iTrader: (6)
Joined: Jan 2005
Posts: 4,659
Likes: 0
From: ludlow, pa
how many actually "tin" your wire before.....
soldering??
im trying to avoid oxidization (turning green) and breaking off or getting bad connections....
this is for soldering copper wire of course.
do i need to "tin" to avoid this? i always use shrink wrap and heat the copper allowing the solder to "flow" into the wires to not make a ball or solder on the copper but to actually get it to flow inside the copper joints....
so what am i doing wrong?
im not tinning these BTW...
im trying to avoid oxidization (turning green) and breaking off or getting bad connections....
this is for soldering copper wire of course.
do i need to "tin" to avoid this? i always use shrink wrap and heat the copper allowing the solder to "flow" into the wires to not make a ball or solder on the copper but to actually get it to flow inside the copper joints....
so what am i doing wrong?
im not tinning these BTW...
#2
Always tin the wires first. It will keep the ends from fraying and make everything look that much nicer. Make sure you twist the ends of the wires together, then solder the joint.
Tin. Twist. Solder. Shrink Wrap.
Tin. Twist. Solder. Shrink Wrap.
#4
Engine, Not Motor
iTrader: (1)
Joined: Feb 2001
Posts: 29,793
Likes: 119
From: London, Ontario, Canada
I never tin my wire. I do make sure it's quite clean before making the joint.
However I use a high quality flux cored solder. The flux cleans as the solder melts.
I keep my soldering tip well tinned and very clean, however.
Another important point is to clean all the flux off of the wire before you heat shrink the joint. Flux left on will corrode the joint in time.
However I use a high quality flux cored solder. The flux cleans as the solder melts.
I keep my soldering tip well tinned and very clean, however.
Another important point is to clean all the flux off of the wire before you heat shrink the joint. Flux left on will corrode the joint in time.
#6
I agree with Aaron Cake. If you're worried about corrosion, you need to clean the flux off the solder joint after soldering.
"What flux?" you might ask? Most solder contains flux, it helps the solder flow. Flux usually has a yellow tint to it, and is a bit sticky when it dries. Burnt flux will sometimes turn brown or black. Flux will corrode over time and eat through the solder, an old joint that has been corroded by flux will appear to have a coating of white or yellow powder.
Use rubbing alcohol and a brush with stiff bristles.
Dip the brush in rubbing alcohol and scrub the solder joint, the alcohol dissolves the flux.
Wipe the alcohol/flux mixture away with a soft dry cloth (Q-tips work for this also). A solder joint that has had the flux cleaned will shine brighter and have a nice silver hue (without hints of yellow or brown).
Personally, I don't usually tin wires if they are going to be soldered to other wires, I prefer to wrap them together so they can't pull apart when the solder is hot. IMHO, tinning wires first sometimes makes it more difficult to keep the wires aligned properly when the solder is liquid.
Here's a good soldering how-to video. It emphasizes working with circuit boards, but contains good advice about cleaning flux and general soldering practice.
http://www.curiousinventor.com/guides/How_To_Solder
"What flux?" you might ask? Most solder contains flux, it helps the solder flow. Flux usually has a yellow tint to it, and is a bit sticky when it dries. Burnt flux will sometimes turn brown or black. Flux will corrode over time and eat through the solder, an old joint that has been corroded by flux will appear to have a coating of white or yellow powder.
Use rubbing alcohol and a brush with stiff bristles.
Dip the brush in rubbing alcohol and scrub the solder joint, the alcohol dissolves the flux.
Wipe the alcohol/flux mixture away with a soft dry cloth (Q-tips work for this also). A solder joint that has had the flux cleaned will shine brighter and have a nice silver hue (without hints of yellow or brown).
Personally, I don't usually tin wires if they are going to be soldered to other wires, I prefer to wrap them together so they can't pull apart when the solder is hot. IMHO, tinning wires first sometimes makes it more difficult to keep the wires aligned properly when the solder is liquid.
Here's a good soldering how-to video. It emphasizes working with circuit boards, but contains good advice about cleaning flux and general soldering practice.
http://www.curiousinventor.com/guides/How_To_Solder
Last edited by scotty305; 09-06-08 at 04:45 PM.
#7
Or you could use good wire that's got each individual strand already tinned
I've been told by the gent that built my harness whoes been building harness's for racing pro's for the past twenty someodd years that the worst thing that you can do to an electrical connection is solder it. The solder wicks up into the wire itself and no longer allows it to flex. The solder becomes brittle over time and the wire itself breaks. He's had some of his harness's come back to him and the terminal was either pulled out (not his fault) or the wire was broken becuase a repair was done using solder. I used to always solder my connections up until recently.

Trending Topics
#8
I've seen a lot of soldered wires (from cars to paintball to household and so on) and never had a problem with soldered wires being brittle... but i solder like... |---| that much wire... so it does not need to bend and make turns etc... i can see it maybe being a problem if you solder |--------------| that much, and need it to make turns and bends etc. into crammed spaces.
Use good wires, and good solder and you should not have problems.
Use good wires, and good solder and you should not have problems.
#10
I've seen a lot of soldered wires (from cars to paintball to household and so on) and never had a problem with soldered wires being brittle... but i solder like... |---| that much wire... so it does not need to bend and make turns etc... i can see it maybe being a problem if you solder |--------------| that much, and need it to make turns and bends etc. into crammed spaces.
Use good wires, and good solder and you should not have problems.
Use good wires, and good solder and you should not have problems.
#11
More good reading found here - https://www.rx7club.com/2nd-generation-specific-1986-1992-17/hyperteks-budget-elec-fan-install-811725/
And the MoTeC destruction manual excerpt that I like to reference as well

And the MoTeC destruction manual excerpt that I like to reference as well


#12
http://order.waytekwire.com/productd...IMPING%20TOOL/
Thats the crimping tool I'm using on my TECgt harness to do the connections on the pins for the engine sensors.
Works with a pretty wide ranges of terminals. I've even crimped a few ring terminals on with it.
Wish I'd bought a proper tool years ago...
Thats the crimping tool I'm using on my TECgt harness to do the connections on the pins for the engine sensors.
Works with a pretty wide ranges of terminals. I've even crimped a few ring terminals on with it.
Wish I'd bought a proper tool years ago...
#13
Agreed. Sadly most people will look at that and laugh at the expense. They don't appreciate good tools.
Just to give them something else to laugh at - the crimper that was used for my Deutsch connectors is ~$500. Yes, the crimper.
Just to give them something else to laugh at - the crimper that was used for my Deutsch connectors is ~$500. Yes, the crimper.
#14
http://order.waytekwire.com/productd...IMPING%20TOOL/
Thats the crimping tool I'm using on my TECgt harness to do the connections on the pins for the engine sensors.
Works with a pretty wide ranges of terminals. I've even crimped a few ring terminals on with it.
Wish I'd bought a proper tool years ago...
Thats the crimping tool I'm using on my TECgt harness to do the connections on the pins for the engine sensors.
Works with a pretty wide ranges of terminals. I've even crimped a few ring terminals on with it.
Wish I'd bought a proper tool years ago...
Ever since i got my hands on the snap on crimping tool, I've been happy as hell

http://buy1.snapon.com/catalog/item....re&dir=catalog
#16
^what he said. The one I linked amplifies the leverage...you'd need to have Hulk hands to get the same compression with a regular "plier" style crimper. But they do work good in certain apps.
And I did find them a little tough to get used to, but after 5-6 crimps I think I could conduct a symphony orchestra with them
And I did find them a little tough to get used to, but after 5-6 crimps I think I could conduct a symphony orchestra with them

#17
That is correct, I ended up soldering the cables on the weather pak connectors for the ECU sensors.
^what he said. The one I linked amplifies the leverage...you'd need to have Hulk hands to get the same compression with a regular "plier" style crimper. But they do work good in certain apps.
And I did find them a little tough to get used to, but after 5-6 crimps I think I could conduct a symphony orchestra with them
And I did find them a little tough to get used to, but after 5-6 crimps I think I could conduct a symphony orchestra with them


#18
Strip. Twist. Tin. Solder. Heat Shrink.
I grew up learning from a man who was nasa certified for soldering and has no issue with 402 surface mount parts. Not one thing that I've solder has ever ever ever come back be cause of any type of failure related to where I worked on it. Also trying to factor in a strain relief is one of the best things you can do as an extra precaution.
For crimps I highly suggest getting good quality full cycle crimpers. These will keep you from getting anything besides a perfect crimp. The more money you spend the better the crimp, guaranteed.
I grew up learning from a man who was nasa certified for soldering and has no issue with 402 surface mount parts. Not one thing that I've solder has ever ever ever come back be cause of any type of failure related to where I worked on it. Also trying to factor in a strain relief is one of the best things you can do as an extra precaution.
For crimps I highly suggest getting good quality full cycle crimpers. These will keep you from getting anything besides a perfect crimp. The more money you spend the better the crimp, guaranteed.
#19
soldering does decrease the flexibility of the joint but only marginally if you do it right.
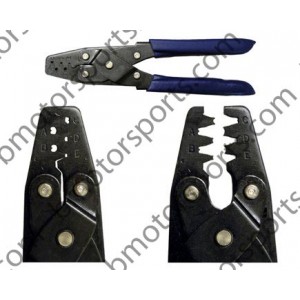
That crimper appears to be an aftermarket replacement for the Delphi tool posted above: http://www.bmotorsports.com/shop/pro...roducts_id/362
do you think there is much difference in quality? It's over $50 cheaper.
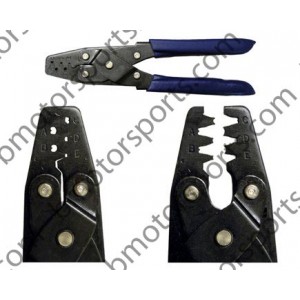
That crimper appears to be an aftermarket replacement for the Delphi tool posted above: http://www.bmotorsports.com/shop/pro...roducts_id/362
do you think there is much difference in quality? It's over $50 cheaper.
#20
That looks exactely like the one I bought from McMaster for ~$30. I like it. Has served me well with all my metri/weather pak connectors. Not for butt connectors though. I have a seperate racheting cycle crimper for butts.
#21
There was a great article in Grass Roots Motorsports a few years ago on just this topic.
The gist of the article: forget soldering, use high quality crimps and tools.
The article may be online.
The gist of the article: forget soldering, use high quality crimps and tools.
The article may be online.
Thread
Thread Starter
Forum
Replies
Last Post
toplessFC3Sman
2nd Generation Specific (1986-1992)
6
03-20-18 02:54 PM