WELDED DIFF WRITEUP for t2 guys
#1
WELDED DIFF WRITEUP for t2 guys

I justwanted to do a quick short write up on how to setup your car with welded diff for those of youwho cant aford 2way lsds and want to drift. after all this work ul love it. and plz dont flame me out, I know some of you are scared of welded and think its scary dangerousand all then dont do it.
First of all, my car is a turbo2 s5, so my drive train is all t2. t2 drive train is different than the s4 NA or s5 NAs . T2s are like twice as beefier in drivetrain and fitment is larger. I believe only NAs came with open diffs, and all t2 models came with lsds[ either vlsd or cluth types]. The problem is a s4 or s5 open diff will not fit in at2 drive train, it wont fit with the t2 halfshafts or drive shaft. So im doing awrite up on how to make it work, just for some of you guys that wanted to go welded but is stuck with a t2.
You will need:
Open diff [from s4 or s5 na models]
s4 or s5 Na halfshafts
17mm socket ratchet and boxend tool
14mm ^^
19mm
breaker bar
pry bar
PB blaster or wd 40
Okay, the best thing to do is make sure you have a backup diff, incase something happens to your welded diff, or if it failed during the welding process.
1. Remove your current diff.
-jack up your car on jack stands, then remove your rear wheels, kee your ebrake up and remove the bottom rear shock with a17mm, and remove the sway bar link 14mm , then remove the halfshafts, its 4 nuts all 14mm, use a open boxend wrench for that. Just pry the halfshafts off, its ezier to pry em off once you have removed the shock and swaybar link. After that, you have to lower your subframe, I think is a 19mm on the twosubframe bolts under your front rear fender wheel well. just unbolt itbut not all theway. then unbolt the link where its holding the subframe, make sure u keep a jack under neath the subframe so itwont drop abrubtly. after the subframe is dropped, you will have access to these diff bolts.

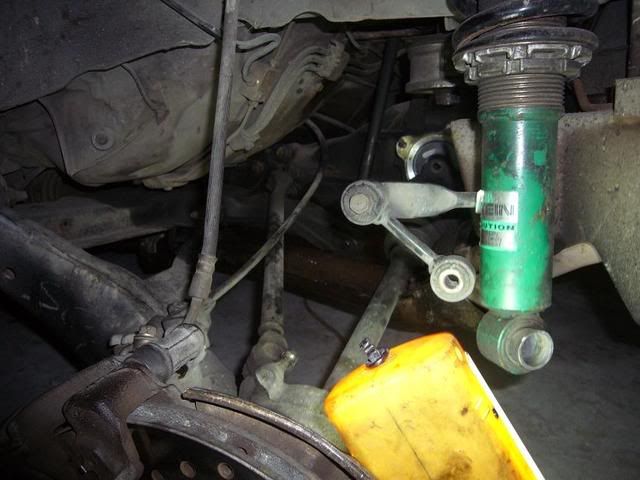
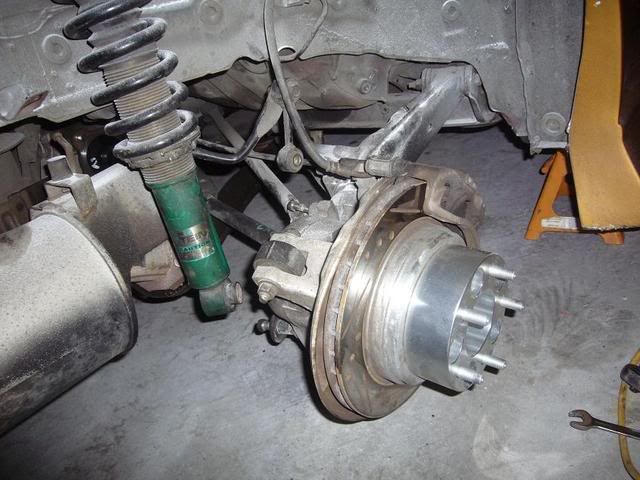
remove the two diff bolts, theres actualy 2 sets of nuts thats easier to get, youll need a 17mm with along extension a breaker bar. once thats unbolted all thats left is the two 17mm nuts on your differential arms. just takes those off, and then get abig prybar, and pry the diff out if it doesnt just fall out. Oh yeah its up to you if you want to disconnect the driveshaft while its in the car, its easier to remove the diff if you disconect the driveshaft, but you dont really have to, it slides out of the tranny.
once you get your diff out, move on to your open diff,unscrew the diffs drain plug and you could either save the gear oil or dispose of it and put new one later. Disassemble the diff with 14mm or 12mm? cant rmemeber, but anyways unbolt all the screws and hammer out the stubshafts then remove the casing.
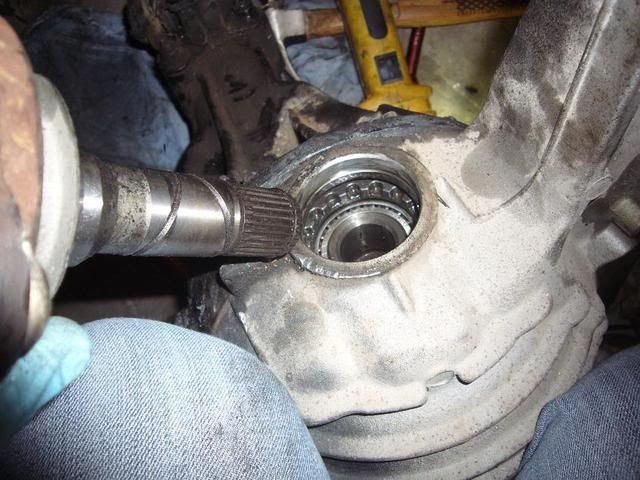
once you do that, remove the diff from the brackets, and keep the half shafts in the diff when you weld it to prevent extra weld from flying in the stubeshafts home. Weld all the spider gears together, and weld the outside gears to the casing. Becareful not to get any welds into the stubshafts. This will take maybe 30minutes of welding, take your time, make sure the welds are nice and strong.

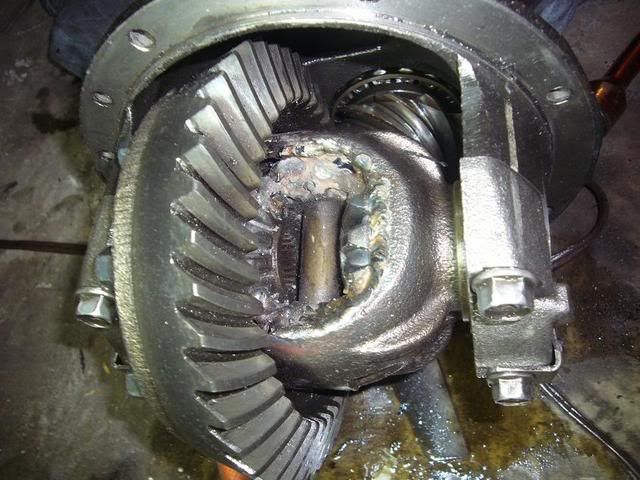
after that let it chill and colll tdown for abit, DO NOT USE WATER to cool it down, itll weaken the steel, just let it air cool. assemble the diff, and I used sillacone sealant for the diff casing, it works good.
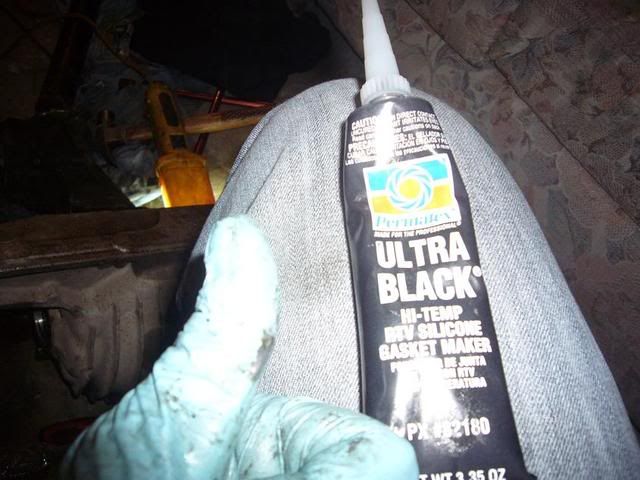
Okay now for the tricky part. The turbo 2 driveshaft will not fit your open diff, nor will a open diffs puny driveshaft fit the t2 tranny. What we need to do, is modifly the t2 driveshaft to fit the open diff. itl become a universal driveshaft for any diff. Its easy, get a dremel or drill and cut the holes inwards. Like this, and check to see if it fits ur diffs stub shaft.
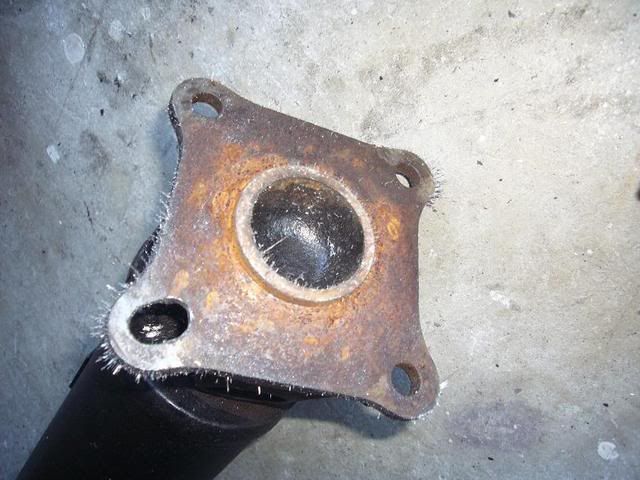
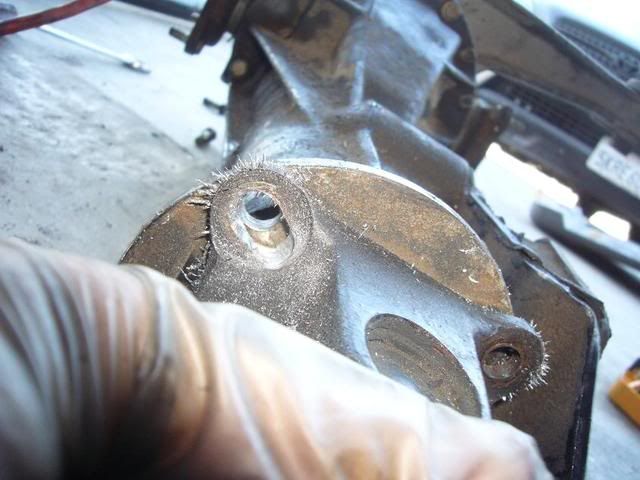
slide your drive shaft into the tranny and slide your diff onto your subframe, bench press it up, and lightly bolt it, dont tighten it yet, make sur eteh subframe is dropped low and carefuly fit the diff in, youll have to fight it alot, sometimes its really hard to fit in, as long as everything is loose, it will be easier to fit. Once its all in just tighten everything up and bolt everything .
The halfshafts, youll need to change to the NA ones. Its easy to remove, with the right tools. you wont need a impact gun, just use abreaker bar , make sure you unlock the bolt first witha small flat head. then hammer the halfshaft out ,careful not to mushroom it, swap the half shafts with the na ones and bolt it together and bam u have awelded setup on ur t2 !
when you initiate, you wont have to hammer the gas like crazy, just feather it at first and be ready to counter steer, and slowly get used to the full lock diff feeling, irecomend powertseering. manual steering is gunna be a bishhh for normal driving and drifting.
well goodluck.
any questions just post.
#4
Wow you welded it with it still attached to the pinion. It is better to take the diff out and put it in a vice so you can work 360deg around it and slag does not get in the ring and pinion gears.
I wonder how long that little ring and pinion will hold power before it breaks.
I wonder how long that little ring and pinion will hold power before it breaks.
#5
Play Well
Joined: Feb 2005
Posts: 4,218
Likes: 0
From: We're all fine here now, thank you. How are you?
Wow you welded it with it still attached to the pinion. It is better to take the diff out and put it in a vice so you can work 360deg around it and slag does not get in the ring and pinion gears.
I wonder how long that little ring and pinion will hold power before it breaks.
I wonder how long that little ring and pinion will hold power before it breaks.
#6
Wow you welded it with it still attached to the pinion. It is better to take the diff out and put it in a vice so you can work 360deg around it and slag does not get in the ring and pinion gears.
I wonder how long that little ring and pinion will hold power before it breaks.
I wonder how long that little ring and pinion will hold power before it breaks.
#7
its ok to weld it while its still in the pumpkin =p
Its an open diff to be welded solid, so you dont wanna take too much time on it, and if you took it apart you would need to check for backlash and all that mess.
shoulda welded this part too

The spider gear to the spin shaft
But should be cool..
I had a nismo 2way lsd, i think i used some heavy oil for it heavier then 90 though
Its an open diff to be welded solid, so you dont wanna take too much time on it, and if you took it apart you would need to check for backlash and all that mess.
shoulda welded this part too

The spider gear to the spin shaft
But should be cool..
I had a nismo 2way lsd, i think i used some heavy oil for it heavier then 90 though
Trending Topics
#8
Wow you welded it with it still attached to the pinion. It is better to take the diff out and put it in a vice so you can work 360deg around it and slag does not get in the ring and pinion gears.
I wonder how long that little ring and pinion will hold power before it breaks.
I wonder how long that little ring and pinion will hold power before it breaks.


#11
Play Well
Joined: Feb 2005
Posts: 4,218
Likes: 0
From: We're all fine here now, thank you. How are you?
#14
I'm running 90w-140 or whatever in my welded right now... I think it might be too thick! I figured I'd run thick stuff because it will get very hot since it's a welded. I'm not getting very much gear noise at all and I have solid diff mounts, so it might be fine.
Opinions?
Opinions?
#15
im running 80 90 w , its the spec for stock open diffs, I guess it feels alrite. Ive been daily driving since welded, its running great. YOU GUYS BETTER KNOCK ON WOOD LOL your trying to curse me LOL !!!

#16
Good writup but i agree with t2rotor when i say those welds are ugly.
I would have packed that bitch full of weld....both sides....on med-high heat and anti-spatter on everything. I would have spent alot longer than 30 minutes welding small sections and then allowing the diff to cool off a little bit (but not too much) before starting again. I might do mine in a week or so.
Here's another good write-up. It's for a 240 but they have pretty much the same guts as an open fc diff...... The welding is sub-par birdshit but the coverage is good.
http://rds.yahoo.com/_ylt=A0geu44Nzx...m/%3fq=node/25
Yes, i'm considering a welded diff. I'm not baller. I will go full 2 way but not any time soon.
P.S. It's SLAG. Not sahg, sag or whatever it is people like to call it these days..... Again, anti-spatter is your friend and you should protect everything and anything from spatter and distortion by any means possible.
I would have packed that bitch full of weld....both sides....on med-high heat and anti-spatter on everything. I would have spent alot longer than 30 minutes welding small sections and then allowing the diff to cool off a little bit (but not too much) before starting again. I might do mine in a week or so.
Here's another good write-up. It's for a 240 but they have pretty much the same guts as an open fc diff...... The welding is sub-par birdshit but the coverage is good.
http://rds.yahoo.com/_ylt=A0geu44Nzx...m/%3fq=node/25
Yes, i'm considering a welded diff. I'm not baller. I will go full 2 way but not any time soon.
P.S. It's SLAG. Not sahg, sag or whatever it is people like to call it these days..... Again, anti-spatter is your friend and you should protect everything and anything from spatter and distortion by any means possible.
Last edited by NoPistons!; 11-08-08 at 12:46 PM.
#17
Play Well
Joined: Feb 2005
Posts: 4,218
Likes: 0
From: We're all fine here now, thank you. How are you?
Good writup but i agree with t2rotor when i say those welds are ugly.
I would have packed that bitch full of weld....both sides....on med-high heat and anti-spatter on everything. I would have spent alot longer than 30 minutes welding small sections and then allowing the diff to cool off a little bit (but not too much) before starting again. I might do mine in a week or so.
Here's another good write-up. It's for a 240 but they have pretty much the same guts as an open fc diff...... The welding is sub-par birdshit but the coverage is good.
http://rds.yahoo.com/_ylt=A0geu44Nzx...m/%3fq=node/25
Yes, i'm considering a welded diff. I'm not baller. I will go full 2 way but not any time soon.
P.S. It's SLAG. Not sahg, sag or whatever it is people like to call it these days..... Again, anti-spatter is your friend and you should protect everything and anything from spatter and distortion by any means possible.
I would have packed that bitch full of weld....both sides....on med-high heat and anti-spatter on everything. I would have spent alot longer than 30 minutes welding small sections and then allowing the diff to cool off a little bit (but not too much) before starting again. I might do mine in a week or so.
Here's another good write-up. It's for a 240 but they have pretty much the same guts as an open fc diff...... The welding is sub-par birdshit but the coverage is good.
http://rds.yahoo.com/_ylt=A0geu44Nzx...m/%3fq=node/25
Yes, i'm considering a welded diff. I'm not baller. I will go full 2 way but not any time soon.
P.S. It's SLAG. Not sahg, sag or whatever it is people like to call it these days..... Again, anti-spatter is your friend and you should protect everything and anything from spatter and distortion by any means possible.
#18
If you're a welder, atleast use proper terminology.
Sag, imo would be when you try to bullshit gap weld on high heat and the weld and whatever it is your welding starts to melt excessively and sags.
Only reason i brough it up is because i've seen it on other forums as well as on the link i posted.
Sag, imo would be when you try to bullshit gap weld on high heat and the weld and whatever it is your welding starts to melt excessively and sags.
Only reason i brough it up is because i've seen it on other forums as well as on the link i posted.
#19
On the fasttrack!
iTrader: (22)
Joined: Oct 2006
Posts: 2,494
Likes: 2
From: virginia beach, virginia
um.........maybe this post is pointless. and i guess im just one of the multi million that believes that one tires spinning a tad faster than the other is good on occasion. for a track car, sure, why not, if youre too broke. for a street car...........slap yourself.
anyways, the other thought i had, its called a differential pinion shaft.
Lloyd
anyways, the other thought i had, its called a differential pinion shaft.
Lloyd
#20
ive had welded diffs in s13 for a long time. never broke.
i had a welded na diff in my t2 and sheered all the teeth off the ring gear after the very first event.
and to all the guys saying it will only last 200-500 miles... thats a lot of track time if you trailer your car and if done right your diff will def last for a long time. ran 2 complete seasons in different s13s but the same diff. never worried about it breaking and still dont and it still hasnt.
i had a welded na diff in my t2 and sheered all the teeth off the ring gear after the very first event.
and to all the guys saying it will only last 200-500 miles... thats a lot of track time if you trailer your car and if done right your diff will def last for a long time. ran 2 complete seasons in different s13s but the same diff. never worried about it breaking and still dont and it still hasnt.
#23
#25
most muffler shops would charge like 10-15 bux to weld it.Unless you have a friend or friends dad that welds it would be perfect.
Yeah I can tell you its going to be a new experience jumping from open to welded... But I think its a fast way to learn
Last edited by dkwasherexd; 11-25-08 at 01:20 PM.