FJO's hsv
#1
FJO's hsv
I noticed quite a few people on here are running FJO's high speed valve, with or without the rest of their stuff. I am in the process of choosing a valve; since FJO's is the cheapest, I will of course be considering theirs. I will be using this to control it. It converts a 0-5v signal into PWM. I've modified it so that I can alter its operating frequency. Here are a few of my concerns about FJO's hsv:
1. What the heck is up with the amperage draw rating? I saw someone mention 8 Amps max? That's ridiculous... Is that for real?
2. FJO mentioned some sort of necessary "driver module" (CWD0082). Are they just trying to make me buy their controller, or will I really need something of this sort?
3. I know the recommended freq and min dc is 30-50 hz, 10% dc. Does anyone have any experience with how well the valve performs at 50hz, 10% dc? I am doubtful of how "high speed" the valve really is...
4. I'm using different sized tubing. What kind of fitting will I need (looks like 1/8" npt male)?
Thanks for reading. I look forward to all of your input.
1. What the heck is up with the amperage draw rating? I saw someone mention 8 Amps max? That's ridiculous... Is that for real?
2. FJO mentioned some sort of necessary "driver module" (CWD0082). Are they just trying to make me buy their controller, or will I really need something of this sort?
3. I know the recommended freq and min dc is 30-50 hz, 10% dc. Does anyone have any experience with how well the valve performs at 50hz, 10% dc? I am doubtful of how "high speed" the valve really is...
4. I'm using different sized tubing. What kind of fitting will I need (looks like 1/8" npt male)?
Thanks for reading. I look forward to all of your input.
Last edited by nilo; 03-24-08 at 01:02 AM.
#2
1. I really don't think it draws 8 amps.
2. If it really draws 8 Amp, you will need their "peak and hold" driver for sure. There are a few people here using it, all you need to ask them to measure the resistance.
3. If the recommend frequency is between 30Hz to 50Hz. 10% dc at 50Hz (20ms) = 2ms. It looks like the valve's opening speed is 2ms.
4. Not sure.
2. If it really draws 8 Amp, you will need their "peak and hold" driver for sure. There are a few people here using it, all you need to ask them to measure the resistance.
3. If the recommend frequency is between 30Hz to 50Hz. 10% dc at 50Hz (20ms) = 2ms. It looks like the valve's opening speed is 2ms.
4. Not sure.
#5
Trending Topics
#11
There is no reason a nitrous solenoid wouldn't necessarily work good for alcohol injection.
Even if all they did was take and off the shelf item (I'm not saying thats what they did) and test it for a year thats still a perfectly legit thing to do.
Even if all they did was take and off the shelf item (I'm not saying thats what they did) and test it for a year thats still a perfectly legit thing to do.
#13
Not FJO related, but does anyone know if a diaphram valve could be PWM'd?
It is a fact, any valve which has fluid in direct contact with any magnetic material, be it magnetic SS or whatever will rust and corrode with either 100% water, or very low mixtures of water/alcohol.
Its seams like a diaphragm valve would be ideal as an HSV if it could open and close fast enough. As there is no magnetic metallic components in contact with the liquid.
Diaphragm valves can be used to switch stuff like sulfuric acid.
as I understand it, the open/close time changes with pressure differential (like any valve I would guess).
It is a fact, any valve which has fluid in direct contact with any magnetic material, be it magnetic SS or whatever will rust and corrode with either 100% water, or very low mixtures of water/alcohol.
Its seams like a diaphragm valve would be ideal as an HSV if it could open and close fast enough. As there is no magnetic metallic components in contact with the liquid.
Diaphragm valves can be used to switch stuff like sulfuric acid.
as I understand it, the open/close time changes with pressure differential (like any valve I would guess).
#14
I know a few diapgragm for isolated valves (wetted part) but not very good for PWM usage. It is normally used for dispensing chemical and medical usage. lee product make such valves.
In order for a PWM to work accurately, it has to be a full-swinging construction. Diaphragm or proportion valve opens progressively by natural. Speeding it up will not change its characteristics.
Imagine a water tap, winding it open and winding it shut quickly will be make it open and shut like a gate valve. It is the progressive natural that makes it unsuitable for PWM usage. However, it will work within a narrow range.
Another aspect that makes it veru unlinear to switching: inductance is higher than the true PWM valve, high indiuctance resist fast switching. Secondly, magneting material tends to have a widen BH-curve loop. Current induced ramp-up and ramp-down has follows a different curve.
Even with the best will in the world, you just cannot change the above inbuilt characteristic. PWM valve is for PWM usage and proportional valve is for a delivery system with complex electromechanical feedback loop.
I am sorry to dwell on the subject. I think you are OK, the FJO valve is a true PWM valve.
In order for a PWM to work accurately, it has to be a full-swinging construction. Diaphragm or proportion valve opens progressively by natural. Speeding it up will not change its characteristics.
Imagine a water tap, winding it open and winding it shut quickly will be make it open and shut like a gate valve. It is the progressive natural that makes it unsuitable for PWM usage. However, it will work within a narrow range.
Another aspect that makes it veru unlinear to switching: inductance is higher than the true PWM valve, high indiuctance resist fast switching. Secondly, magneting material tends to have a widen BH-curve loop. Current induced ramp-up and ramp-down has follows a different curve.
Even with the best will in the world, you just cannot change the above inbuilt characteristic. PWM valve is for PWM usage and proportional valve is for a delivery system with complex electromechanical feedback loop.
I am sorry to dwell on the subject. I think you are OK, the FJO valve is a true PWM valve.
#15
I have made quiet a few typos and grammar mistakes, please ignore the above thread and read this one... It was done in one early hours of the morning.
I know a few diaphragm isolated valves makers (wetted part) but not very good for PWM usage. It is normally used for dispensing chemical and medical usage. "Lee products" makes such valves.
In order for a PWM to work accurately, it has to be a full-swinging action construction. Diaphragm or proportion valve opens progressively by natural. Speeding it up will not change its characteristics.
Imagine a water tap, winding it open and winding it shut quickly will not make it open and shut like a gated valve. It is the progressive natural that makes it unsuitable for PWM usage. (think of the opening period as a trangular wave rather a square wave). However, it will work within a narrow range.
Another aspect that makes it very unlinear to switching: inductance is higher than the true PWM valve, high inductance resists fast switching. Secondly, magneting material tends to have a effective wider BH-curve loop whem operating in the unsturated mode. Current that ramp-up and ramp-down follows a different curve, it is called the hysteresis.
Even with the best will in the world, you just cannot change the above inbuilt characteristic. PWM valve is for PWM usage and proportional valve is for a delivery system with complex electro/mechanical feedback loop.
I am sorry to dwell on the subject. I think you are OK, the FJO valve is a true PWM valve.
I know a few diaphragm isolated valves makers (wetted part) but not very good for PWM usage. It is normally used for dispensing chemical and medical usage. "Lee products" makes such valves.
In order for a PWM to work accurately, it has to be a full-swinging action construction. Diaphragm or proportion valve opens progressively by natural. Speeding it up will not change its characteristics.
Imagine a water tap, winding it open and winding it shut quickly will not make it open and shut like a gated valve. It is the progressive natural that makes it unsuitable for PWM usage. (think of the opening period as a trangular wave rather a square wave). However, it will work within a narrow range.
Another aspect that makes it very unlinear to switching: inductance is higher than the true PWM valve, high inductance resists fast switching. Secondly, magneting material tends to have a effective wider BH-curve loop whem operating in the unsturated mode. Current that ramp-up and ramp-down follows a different curve, it is called the hysteresis.
Even with the best will in the world, you just cannot change the above inbuilt characteristic. PWM valve is for PWM usage and proportional valve is for a delivery system with complex electro/mechanical feedback loop.
I am sorry to dwell on the subject. I think you are OK, the FJO valve is a true PWM valve.
#16
This is sort of on topic.
Being ignorant and thinking my FJO nozzle is a 500hp (500cc?) it didn't take to long to go through 4 litres. I guess I'm going to need a bigger tank eventually or really only use this for drag racing which I never do?
Any idea how long a jug of windsheild fluid should last?
thanks.
Being ignorant and thinking my FJO nozzle is a 500hp (500cc?) it didn't take to long to go through 4 litres. I guess I'm going to need a bigger tank eventually or really only use this for drag racing which I never do?
Any idea how long a jug of windsheild fluid should last?
thanks.
#17
Racing Rotary Since 1983
iTrader: (6)
Joined: Oct 2001
Posts: 6,136
Likes: 563
From: Florence, Alabama
Ian,
if you have one FJO 500 solenoid i assume you have a 500 CC/Min solenoid. i don't recall your setup or what you are trying to accomplish but if you refer to a sticky thread you will get an idea as to sizing.
500 would be fine for water. generally if you are just trying to reduce/eliminate knock 300 to 500 works.
if you are trying to make lots of hp and are "tuning up" (that is removing base fuel and replacing it w methanol) you will want more delivery.
for instance: 2 850 and 2 1600 fuel injectors produce 4900 cc/min max. since there are less BTUs in alcohol per volume you need remove around 350 CC of pump if you deliver 500 CC w your FJO solenoid. not much of an impact.
i ran 1260 CC/min w my alkycontrol system, i now have the full FJO system w 2 700 CC/Min FJO solenoids.
i run a 4 gallon fuel cell and consider 4 gallons to be about right...
hc
if you have one FJO 500 solenoid i assume you have a 500 CC/Min solenoid. i don't recall your setup or what you are trying to accomplish but if you refer to a sticky thread you will get an idea as to sizing.
500 would be fine for water. generally if you are just trying to reduce/eliminate knock 300 to 500 works.
if you are trying to make lots of hp and are "tuning up" (that is removing base fuel and replacing it w methanol) you will want more delivery.
for instance: 2 850 and 2 1600 fuel injectors produce 4900 cc/min max. since there are less BTUs in alcohol per volume you need remove around 350 CC of pump if you deliver 500 CC w your FJO solenoid. not much of an impact.
i ran 1260 CC/min w my alkycontrol system, i now have the full FJO system w 2 700 CC/Min FJO solenoids.
i run a 4 gallon fuel cell and consider 4 gallons to be about right...
hc
#18
Ian,
if you have one FJO 500 solenoid i assume you have a 500 CC/Min solenoid. i don't recall your setup or what you are trying to accomplish but if you refer to a sticky thread you will get an idea as to sizing.
500 would be fine for water. generally if you are just trying to reduce/eliminate knock 300 to 500 works.
if you are trying to make lots of hp and are "tuning up" (that is removing base fuel and replacing it w methanol) you will want more delivery.
for instance: 2 850 and 2 1600 fuel injectors produce 4900 cc/min max. since there are less BTUs in alcohol per volume you need remove around 350 CC of pump if you deliver 500 CC w your FJO solenoid. not much of an impact.
i ran 1260 CC/min w my alkycontrol system, i now have the full FJO system w 2 700 CC/Min FJO solenoids.
i run a 4 gallon fuel cell and consider 4 gallons to be about right...
hc
if you have one FJO 500 solenoid i assume you have a 500 CC/Min solenoid. i don't recall your setup or what you are trying to accomplish but if you refer to a sticky thread you will get an idea as to sizing.
500 would be fine for water. generally if you are just trying to reduce/eliminate knock 300 to 500 works.
if you are trying to make lots of hp and are "tuning up" (that is removing base fuel and replacing it w methanol) you will want more delivery.
for instance: 2 850 and 2 1600 fuel injectors produce 4900 cc/min max. since there are less BTUs in alcohol per volume you need remove around 350 CC of pump if you deliver 500 CC w your FJO solenoid. not much of an impact.
i ran 1260 CC/min w my alkycontrol system, i now have the full FJO system w 2 700 CC/Min FJO solenoids.
i run a 4 gallon fuel cell and consider 4 gallons to be about right...
hc
My intentions was to improve buttom end grunt and be able to run 20+psi on pump gas when needed. Its a combo 50/50 ie windsheild fluid injection. Figure turn on at 10psi or something. Have not figured out the details and may leave it up to the tuner. I know I would like to run my standard 15psi on pump fuel without AI if needed. Just have a separate map with more power (Advanced ign and such) when I am running A/I.
I gather in the future a bigger tank will be required.
Thanks for your input.
#19
Howard, I've got my 240z setup with one FJO 700 cc/min injector. My horsepower range is 360ish to the wheels (nothing like your monster) and I am using 6 440cc injectors for primary fueling.
Have you maxed out the DC of the FJO injector? What DCs are you seeing with their standalone? I am using the Wolf V500 to control the injector via an auxiliary PWM channel.
Preliminary calcs show that at 20 psi I will be very close to 100% DC at 4000 rpm.
Have you maxed out the DC of the FJO injector? What DCs are you seeing with their standalone? I am using the Wolf V500 to control the injector via an auxiliary PWM channel.
Preliminary calcs show that at 20 psi I will be very close to 100% DC at 4000 rpm.
#20
Racing Rotary Since 1983
iTrader: (6)
Joined: Oct 2001
Posts: 6,136
Likes: 563
From: Florence, Alabama
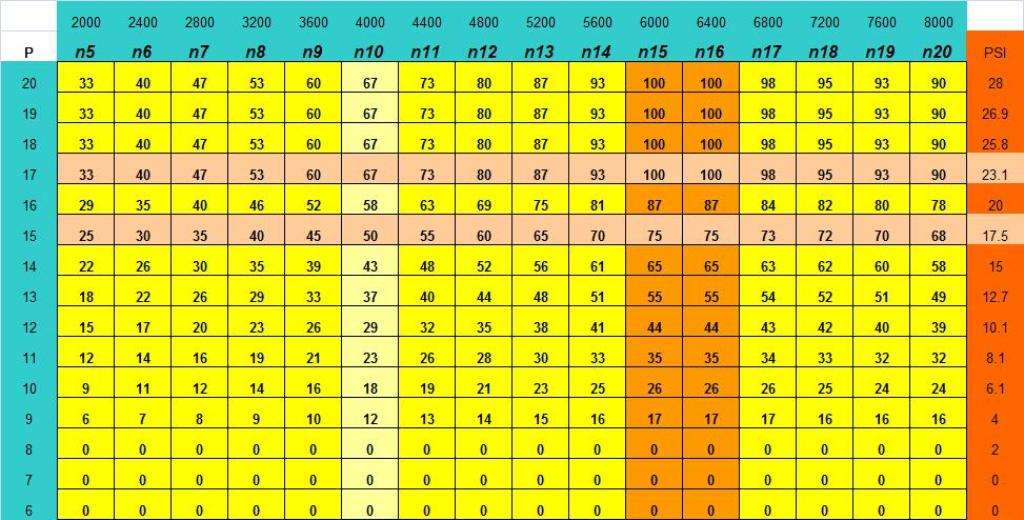
here's an XL spreadsheet workup of what i have loaded into my FJO controller. as you can see delivery is expressed and commanded in terms of % of max solenoid output.
my objective is to be running max (for my 2 700 CC solenoids) alcohol at max torque and then tune around that number w base fuel. this is in the neighborhood of what i ran deliverywise w my Alkycontrol setup.
ktm240Z.. what are you running for injectant? just as an FYI, rotaries use approx 30% more airflow and fuel to make equivalent piston hp. engines use max fuelflow per combustion event around peak torque. note my delivery decreases after 6400. so maxxing out around 4000 might work...
hc
#21
Howard, I will be running 100% meth as an injectant. My peak torque is at 4250ish, so maxing out around that point is no surprise and I expected to as a matter of fact. My main concern really is running 100% DC.
As you have stated before (and as it typically recommended for EFI systems), you typically tune for 75% to 80% DC for your fuel injectors. Running them at 100% DC is just asking for trouble. I am taking the same logic and applying it to the FJO setup. Is 100% DC a problem?
Also, I note that your are at 100% DC from 23 psi on. Anything past 23 psi and you will be running replacing less than 20% meth.
As you have stated before (and as it typically recommended for EFI systems), you typically tune for 75% to 80% DC for your fuel injectors. Running them at 100% DC is just asking for trouble. I am taking the same logic and applying it to the FJO setup. Is 100% DC a problem?
Also, I note that your are at 100% DC from 23 psi on. Anything past 23 psi and you will be running replacing less than 20% meth.
#22
Racing Rotary Since 1983
iTrader: (6)
Joined: Oct 2001
Posts: 6,136
Likes: 563
From: Florence, Alabama
good question re 100%... i will check w FJO and advise.
i run two Garrett TO4s on my setup and they make max airflow between 17 and 23 psi. over 80 pounds per minute. i don't ever expect to run more than 23 psi. i have max base fuel after 23 to protect against overboost lean. i may rethink the alcohol in that area...
hc
i run two Garrett TO4s on my setup and they make max airflow between 17 and 23 psi. over 80 pounds per minute. i don't ever expect to run more than 23 psi. i have max base fuel after 23 to protect against overboost lean. i may rethink the alcohol in that area...
hc
#23
My other concern regarding 100% DC is when you switch from say 95% to 100% in your load cells. What is the response/opening time of the injector? This could result in less than 100% DC flow when needed as the injector has not fully opened.
They say that the minimum DC is 10%. As Richard L with Aquamist has pointed out here and in other forums, the injector opening time plays a significant role. If the injector response time is 2 ms, for instance, that is 4 ms for an open and close cycle. 4 ms at 6500 rpm is 22% DC.....
They say that the minimum DC is 10%. As Richard L with Aquamist has pointed out here and in other forums, the injector opening time plays a significant role. If the injector response time is 2 ms, for instance, that is 4 ms for an open and close cycle. 4 ms at 6500 rpm is 22% DC.....
#24
Keep in mind if you max out your solenoid at 4K (or whatever) rpm as RPM's rise there is no more AI to add, so your percentage is going to drop proportionally with rpm.
As in if you have the solenoid at 100% at 4K rpm and that = a 20% by volume replacement of fuel. At 8K rpm thats going to be a 10% by volume replacement of fuel (or very close, you can. run a little less fuel north of peak tq, but it should be really close).
As in if you have the solenoid at 100% at 4K rpm and that = a 20% by volume replacement of fuel. At 8K rpm thats going to be a 10% by volume replacement of fuel (or very close, you can. run a little less fuel north of peak tq, but it should be really close).
#25
slo, not necessarily. You have to take into account your fueling requirement at the higher RPMs as well. Howard starts pulling fuel past peak torque and so do I. While my RPMs may be rising (and the DC % increasing accordingly), I am also pulling fuel which lowers the DC %.