Pitting in my O-ring grooves! Need advise before I re-use irons
#1
Pitting in my O-ring grooves! Need advise before I re-use irons
After I bead blasted the O-ring grooves in my irons, I noticed several areas where there is some shallow pitting, making the surface a little iffy.
I've never seen this before (i've also never tried glass bead blasting the grooves) and I'm wondering if it's going to cause any problems.
I've never seen this before (i've also never tried glass bead blasting the grooves) and I'm wondering if it's going to cause any problems.

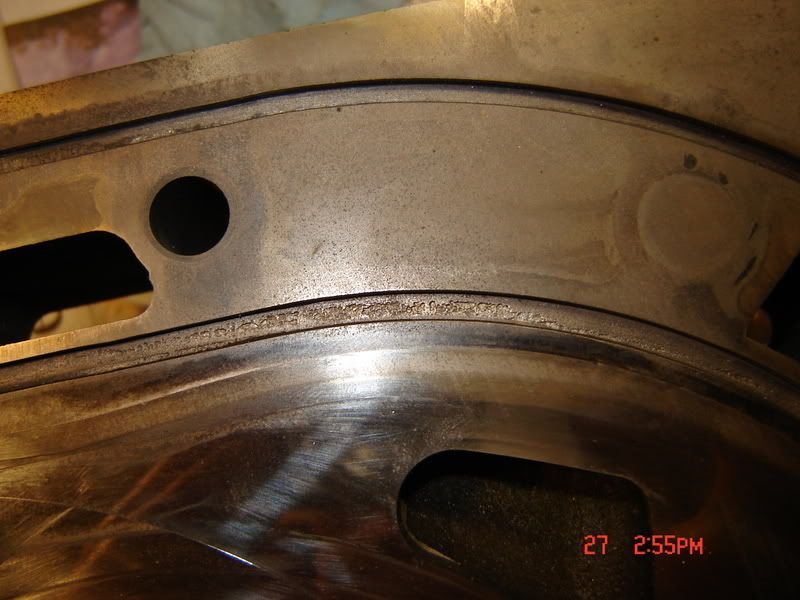
#3
The sad thing is that the irons are perfect otherwise. No warpage and negligible stepped wear. My whole set of irons has a few little spots like this.
What I'm wondering is if any builders have personal experience with irons like this and whether or not they deemed them junk and why.
I was considering JB weld, smoothing it over and flush with the good surface, letting it dry, and then giving it a little wet sand. I have repaired pitting in a rotor husing like this before, but it was nowhere near as large of an area.
What I'm wondering is if any builders have personal experience with irons like this and whether or not they deemed them junk and why.
I was considering JB weld, smoothing it over and flush with the good surface, letting it dry, and then giving it a little wet sand. I have repaired pitting in a rotor husing like this before, but it was nowhere near as large of an area.
#4
I've used irons that looked like that in the past on FC's with no problems. Good thing is it's by the intake port, which is the coolest part of the combustion chamber.
It's your call of course - it is a shame to pitch a perfectly good iron. Using some Devcon or JB Weld might be a worthwhile idea - tape up the surrounding surface, and use a screwdriver the width of the groove to apply it like drywall mud - just let the pits fill up, and remove the excess. Just use little dabs of material at a time, and slowly fill in the pits. It's definitely worth a try - if it doesn't turn out well, pitch it anyhow.
Dale
It's your call of course - it is a shame to pitch a perfectly good iron. Using some Devcon or JB Weld might be a worthwhile idea - tape up the surrounding surface, and use a screwdriver the width of the groove to apply it like drywall mud - just let the pits fill up, and remove the excess. Just use little dabs of material at a time, and slowly fill in the pits. It's definitely worth a try - if it doesn't turn out well, pitch it anyhow.
Dale
#5
Lives on the Forum
iTrader: (8)
Joined: Oct 2003
Posts: 11,576
Likes: 26
From: Morristown, TN (east of Knoxville)
IF you use hylomar or another sealant in the oring groove you'll have no problems with it. You never get leakage on that side, as the o-ring gets crushed when the engine is tensioned and actually seals on 3 sides on the iron. IF you'll recall when you tore the engine down, the seal was seated firmly against the side walls of the iron as well as the "floor" of the groove.
The seal only leaks when it gets violated on the rotorhousing side, where there's only one side to seal against all the pressure. This is why the housing surface is much more important. When reusing used housings with minor surface pitting and imperfection, I use ultra black sealant to take up the small pitting and promote a seal. IF there's a larger pit or hole in the rotorhousing I'll fill it with jb stick weld and then file it down smooth.
IF you refuse to use the iron it's because you're being a perfectionist, or because you're taking the advice of someone who is. IF anyone knows what can and can't be reused, it'd be me, because I reuse a lot of stuff in most of the builds I do. Since I've built hundreds of such engines, with almost perfect success, it's clear there's no flaw with my line of thinking.
The seal only leaks when it gets violated on the rotorhousing side, where there's only one side to seal against all the pressure. This is why the housing surface is much more important. When reusing used housings with minor surface pitting and imperfection, I use ultra black sealant to take up the small pitting and promote a seal. IF there's a larger pit or hole in the rotorhousing I'll fill it with jb stick weld and then file it down smooth.
IF you refuse to use the iron it's because you're being a perfectionist, or because you're taking the advice of someone who is. IF anyone knows what can and can't be reused, it'd be me, because I reuse a lot of stuff in most of the builds I do. Since I've built hundreds of such engines, with almost perfect success, it's clear there's no flaw with my line of thinking.
#6
Alright, I'll stop being so damn picky. After all, the car has to get finished someday. 
Thanks everyone, I really appreciate the feedback. I'll try my hand at some JB weld.

Thanks everyone, I really appreciate the feedback. I'll try my hand at some JB weld.
Trending Topics
#8
Yeah, I'm just going to use hylomar and not even bother with the JB weld. I think it might cause problems down the road if it were to lose it's adhesion to the iron.
I already picked up a large tube on eBay from the UK a while ago in anticipation of this rebuild. "Hylomar Universal Blue"... I put that **** on my eggo waffles in the morning.
Originally Posted by GoodfellaFD3S
I definitely recommend using hylomar on the coolant o-rings for install. It can be tough to find, but the stuff works great!
Thread
Thread Starter
Forum
Replies
Last Post
eplusz
General Rotary Tech Support
15
10-07-15 05:04 PM