Mazda: FD's compressor surge from the factory
#1
Mazda: FD's compressor surge from the factory
Ok so this is weird.
Apparently all the service manuals and technical documents are missing some information about how the stock twins work. It turns out that Mazda found the best turbo transition is achieved when the secondary turbo continuously runs in a straight up surge condition as it is about to come online. A surge condition is when the compressed air is actually moving backwards through the piping and working against the compressor wheel as it is being spun up.
During prespool of the secondary turbo, there is a period of time when the charge control valve is closed and the charge relief valve is open. The charge control valve blocks the secondary turbo's compressed air from getting into the engine. The charge relief vents that air back into the airbox. This much we all knew, and it is documented in multiple places.
Well according to two Mazda papers I have acquired, both the charge relief valve and the charge control valve are closed right before the secondary turbo comes online. The engine is still feeding the secondary turbine wheel exhaust gas, but the compressed air has nowhere to go but backwards. Counter-intuitively, compressor surge actually allowed the secondary turbo to get up to speed faster.

Mazda tested how much continuous surging the secondary turbo could take. This particular test data is actually from the 20B, but the idea is the same.

In this test data the secondary turbo could run in a surge condition for almost 10 seconds before the charge temps and the turbo itself would significantly heat up. This testing was all part of an effort to figure out an optimal control strategy that minimizes boost drop during transition while maintaining longevity of the turbo.
So I guess all this is really just FD trivia. It does show that "real" engineers have a more complex understanding of engines and turbochargers than the simple black-and-white rules that circulate the internet.
Apparently all the service manuals and technical documents are missing some information about how the stock twins work. It turns out that Mazda found the best turbo transition is achieved when the secondary turbo continuously runs in a straight up surge condition as it is about to come online. A surge condition is when the compressed air is actually moving backwards through the piping and working against the compressor wheel as it is being spun up.
During prespool of the secondary turbo, there is a period of time when the charge control valve is closed and the charge relief valve is open. The charge control valve blocks the secondary turbo's compressed air from getting into the engine. The charge relief vents that air back into the airbox. This much we all knew, and it is documented in multiple places.
Well according to two Mazda papers I have acquired, both the charge relief valve and the charge control valve are closed right before the secondary turbo comes online. The engine is still feeding the secondary turbine wheel exhaust gas, but the compressed air has nowhere to go but backwards. Counter-intuitively, compressor surge actually allowed the secondary turbo to get up to speed faster.

Mazda tested how much continuous surging the secondary turbo could take. This particular test data is actually from the 20B, but the idea is the same.

In this test data the secondary turbo could run in a surge condition for almost 10 seconds before the charge temps and the turbo itself would significantly heat up. This testing was all part of an effort to figure out an optimal control strategy that minimizes boost drop during transition while maintaining longevity of the turbo.
So I guess all this is really just FD trivia. It does show that "real" engineers have a more complex understanding of engines and turbochargers than the simple black-and-white rules that circulate the internet.
#2
I am always amazed with the contributions you make to this forum
.
Whenever I see a thread and you are the OP I always click on it and everytime I learn something.
My question is; where did you get this data from if none of the public published manuals have this info?
Is there any documentation that gives a set amount of time the CRV and the CCV are closed prior to transition?
The sequential system in this car always impresses me.
Thanks for the info.
John

Whenever I see a thread and you are the OP I always click on it and everytime I learn something.
My question is; where did you get this data from if none of the public published manuals have this info?
Is there any documentation that gives a set amount of time the CRV and the CCV are closed prior to transition?
The sequential system in this car always impresses me.
Thanks for the info.
John
#4
I remember reading on this forum that the secondary turbo usually goes bad before the primary turbo. Most people say it is because of heat, could the compressor surge be another contributing factor to the secondary turbo going bad first?
John
John
#5
I can vouch for that, I have replaced my secondary turbo 3 times In Two years and the primary turbo only once.. I got so tired of playing games with the twins I just gave up on them all together.
#6
One thing I am reassessing is whether the PFC uses this same type of control logic to control the charge relief valve. It is likely that only the stock ECU creates the surge condition and the PFC does not. In my previous testing I found that the PFC's control logic mirrors what the service manuals say. The problem is that the workshop manual and service highlights aren't completely correct when viewed in light of this new data. The manuals were intended to familiarize technicians with how the systems work but they are not to be taken as a full technical treatise.
#7
Based on this new data I can already see that the PFC's control logic is inferior to the stock ECU's. For example, the stock ECU has a separate control mode for 1st gear to optimize transition:

Now compare the operation chart from the FD workshop manual to this new operational diagram

I always argued that the charge control, charge relief, and turbo control solenoids were all intended to switch at a fixed "turbo transition" point. The manuals imply this in multiple places, and the PFC operates in essentially the same fashion based on my data logging. The real system is more complicated.

While the secondary turbo is spinning up from the precontrol system, the charge relief valve suddenly closes. The secondary turbo goes into a surge condition. The turbo control valve begins to open and even more exhaust feeds the secondary turbo while it's in surge. Finally, the charge control valve opens last. So the twins are even more complicated and the stock ECU is IMO better engineered for spool than we thought.
Coming back to this question of whether the secondary turbo fails more frequently due to the intentional compressor surging: Since it is unlikely that the PFC uses that logic, and lots of people with frequent turbo failures are running a PFC, there is a good chance that the compressor surging is not some kind of "smoking gun".

Now compare the operation chart from the FD workshop manual to this new operational diagram

I always argued that the charge control, charge relief, and turbo control solenoids were all intended to switch at a fixed "turbo transition" point. The manuals imply this in multiple places, and the PFC operates in essentially the same fashion based on my data logging. The real system is more complicated.

While the secondary turbo is spinning up from the precontrol system, the charge relief valve suddenly closes. The secondary turbo goes into a surge condition. The turbo control valve begins to open and even more exhaust feeds the secondary turbo while it's in surge. Finally, the charge control valve opens last. So the twins are even more complicated and the stock ECU is IMO better engineered for spool than we thought.
Coming back to this question of whether the secondary turbo fails more frequently due to the intentional compressor surging: Since it is unlikely that the PFC uses that logic, and lots of people with frequent turbo failures are running a PFC, there is a good chance that the compressor surging is not some kind of "smoking gun".
Trending Topics
#8
I agree that engineers get a bad rap in just about every industry. Of course no design is perfect, and the engineers get shot up for all kinds of trivia and stuff that they may have had little control over, and there are countless successes that nobody even knows about.
David
#10
The stock ECU knows when you're in neutral, 1st gear, and 2nd gear. Consequently, it also knows if you're in a higher gear (3rd, 4th, 5th), but can't distinguish between them.
Perhaps a little off-topic, but since we're talking about the factory ECU, I recently found out that during boost-induced fuel cut, the stock ECU only cuts fuel to the rear rotors and not the front. Not sure if this was common knowledge or not, but I found it interesting.
I have a friend that can definitively test if the charge control and charge relief valves are closed right before transition.
Perhaps a little off-topic, but since we're talking about the factory ECU, I recently found out that during boost-induced fuel cut, the stock ECU only cuts fuel to the rear rotors and not the front. Not sure if this was common knowledge or not, but I found it interesting.
I have a friend that can definitively test if the charge control and charge relief valves are closed right before transition.
#12
Or if you're doing diagnostics, tee into the solenoid output and watch the line with a pressure/vacuum gauge. I did that once but I can't recall the outcome.
David
#13
Yes, but his solution is a little more elegant, but essentially the same concept.
#15
for all intents and purposes it is not possible. the PFC triggers the charge control and charge relief at the same time, and the trigger point is based on the turbo transition setting. technically you could wire up relays, switches, timers, etc but there's really no point in that level of complication, because there's no guarantee it would improve transition significantly. as many of us have resigned ourselves to so many times before, the PFC is about as good as it gets for most plug-and-play applications.
If the FD had been a less expensive, higher volume platform I'm sure somebody would have turned the factory ECU into an easily tuneable system like a Hondata computer. Then we would be able to tinker with it more.
If the FD had been a less expensive, higher volume platform I'm sure somebody would have turned the factory ECU into an easily tuneable system like a Hondata computer. Then we would be able to tinker with it more.
#17
Interesting read. Thanks. Also curious if your eventually able to confirm the control logic question of the PFC.
Weird. Being a dense civil servant with no engineering background, I feel smarter... and dumber at the same time.
Weird. Being a dense civil servant with no engineering background, I feel smarter... and dumber at the same time.
#19
Keep in mind that according to the literature we have, there are two ways the sequential turbos might operate:
1) the workshop manual way, the way we all assumed
2) the "deliberate compressor surge" strategy described in this thread by two Mazda papers
I have a massive thread about this. The PFC behaves according to the workshop manual. from this post: https://www.rx7club.com/showpost.php...4&postcount=31
that analysis did not take into account the information presented in this thread--I was not aware of the "deliberate compressor surge" design at the time. you can see that the PFC matches the workshop manual in its description of how things work (charge contro, charge relief and turbo control switch at the same time). The PFC does not match the description from the Mazda papers, where the charge control opens last. It is the control logic of the factory ECU that will not be easy to confirm. I suppose it's possible that somehow the stock ECU does not behave like those two Mazda papers (one on the 20B one on the 13B) I am referring to here say. I'm not sure if we'll ever really know for sure though.
It could at least do an approximation of the "intentional compressor surge" control strategy. So could a Haltech or anything else with enough adjustable outputs. You need to switch the charge control, charge relief, and turbo control all independently of each other. Then it would have to be coordinated with the precontrol and wastegate. It could be done, but remember that Mazda had modeling, test labs, and $Texas to come up with their calibration.
1) the workshop manual way, the way we all assumed
2) the "deliberate compressor surge" strategy described in this thread by two Mazda papers
I'll put up Sandro's log to illustrate a few things. He goes through transition one time and then stays non sequential for the rest of the run. First, take a look at this description of how the solenoids should operate from the factory:
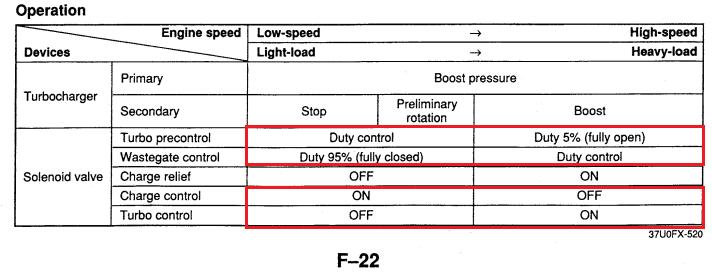
Now here's an excerpt from Sandro's log. Sorry there's so much crap on the screen, I'm trying to get a lot of points across with one screenshot. I am assuming he is using default turbo transition settings.

symbols:
TCN ---> Turbo Control solenoid. A value of "1" means it is energized, "0" means it is not.
CCN ---> Charge control solenoid. A value of "1" means it is energized, "0" means it is not.
PIM ---> Manifold pressure value. 10000 is atmospheric pressure, 20000 is 1.0 kg/cm^2 boost, and any values in between
PC% ---> Precontrol solenoid duty. More duty = actuator more closed (higher boost)
WG% ---> Wastegate solenoid duty. More duty = actuator more closed (higher boost)
TPS V ---> Throttle position sensor voltage. Technically 100% throttle is somewhere between 4.2 and 4.6 volts
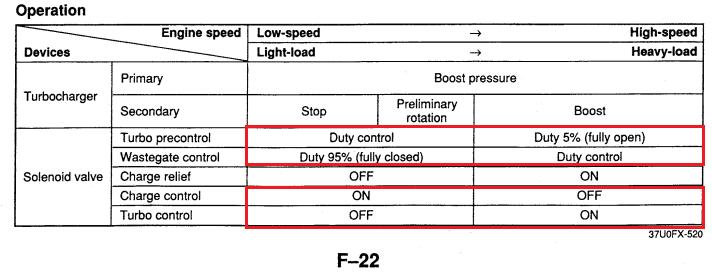
Now here's an excerpt from Sandro's log. Sorry there's so much crap on the screen, I'm trying to get a lot of points across with one screenshot. I am assuming he is using default turbo transition settings.

symbols:
TCN ---> Turbo Control solenoid. A value of "1" means it is energized, "0" means it is not.
CCN ---> Charge control solenoid. A value of "1" means it is energized, "0" means it is not.
PIM ---> Manifold pressure value. 10000 is atmospheric pressure, 20000 is 1.0 kg/cm^2 boost, and any values in between
PC% ---> Precontrol solenoid duty. More duty = actuator more closed (higher boost)
WG% ---> Wastegate solenoid duty. More duty = actuator more closed (higher boost)
TPS V ---> Throttle position sensor voltage. Technically 100% throttle is somewhere between 4.2 and 4.6 volts
It could at least do an approximation of the "intentional compressor surge" control strategy. So could a Haltech or anything else with enough adjustable outputs. You need to switch the charge control, charge relief, and turbo control all independently of each other. Then it would have to be coordinated with the precontrol and wastegate. It could be done, but remember that Mazda had modeling, test labs, and $Texas to come up with their calibration.
#20
the air isn't being pushed back through the turbo it's just that the cavity is filled so the compressor can't fill it anymore. the exhaust is turning the turbine wheel and the compressed air is backing up in the intake piping because it has no where to go causing the surge.
i don't know why so many people say that surging is that bad for the turbos, it's not.
i don't know why so many people say that surging is that bad for the turbos, it's not.
Last edited by RotaryEvolution; 12-14-10 at 12:35 PM.
#21
Surge
This is a very interesting discussion. Was wondering if this surge condition might of been what was casuing the 3K stumble, or part of it. Since moving to a PFC my 3K stumble is completely gone. Also I was planning on building a Car PC that interfaced to the stock ECU, some interesting threads on that, but I no longer use it so stopped that project. But certainly would be worth exploring if enough people were interested. My plan now is to intergrate a car PC with the PFC and use a tocuh screen etc.
#22
surge
HERE is what they failed to tell everybody.
The SEQ. turbo is the best concept ever HOWEVER this design is horrible. To cut a long story short you got two turbos forcing air agaist each other. thats why you get all kind of spikes and motor blowouts.
THE FIX. $$ have a welding guru weld dividers one in between your lower Y-pipe and one mid exhaust manifold. TO seperate your air flow from both turbos into the same direction.
The SEQ. turbo is the best concept ever HOWEVER this design is horrible. To cut a long story short you got two turbos forcing air agaist each other. thats why you get all kind of spikes and motor blowouts.
THE FIX. $$ have a welding guru weld dividers one in between your lower Y-pipe and one mid exhaust manifold. TO seperate your air flow from both turbos into the same direction.

#23
HERE is what they failed to tell everybody.
The SEQ. turbo is the best concept ever HOWEVER this design is horrible. To cut a long story short you got two turbos forcing air agaist each other. thats why you get all kind of spikes and motor blowouts.
THE FIX. $$ have a welding guru weld dividers one in between your lower Y-pipe and one mid exhaust manifold. TO seperate your air flow from both turbos into the same direction.
The SEQ. turbo is the best concept ever HOWEVER this design is horrible. To cut a long story short you got two turbos forcing air agaist each other. thats why you get all kind of spikes and motor blowouts.
THE FIX. $$ have a welding guru weld dividers one in between your lower Y-pipe and one mid exhaust manifold. TO seperate your air flow from both turbos into the same direction.

David
#24
HERE is what they failed to tell everybody.
The SEQ. turbo is the best concept ever HOWEVER this design is horrible. To cut a long story short you got two turbos forcing air agaist each other. thats why you get all kind of spikes and motor blowouts.
THE FIX. $$ have a welding guru weld dividers one in between your lower Y-pipe and one mid exhaust manifold. TO seperate your air flow from both turbos into the same direction.
The SEQ. turbo is the best concept ever HOWEVER this design is horrible. To cut a long story short you got two turbos forcing air agaist each other. thats why you get all kind of spikes and motor blowouts.
THE FIX. $$ have a welding guru weld dividers one in between your lower Y-pipe and one mid exhaust manifold. TO seperate your air flow from both turbos into the same direction.

#25
All out Track Freak!
iTrader: (263)
Joined: Jul 2001
Posts: 10,672
Likes: 412
From: Charlottesville VA 22901
HERE is what they failed to tell everybody.
The SEQ. turbo is the best concept ever HOWEVER this design is horrible. To cut a long story short you got two turbos forcing air agaist each other. thats why you get all kind of spikes and motor blowouts.
THE FIX. $$ have a welding guru weld dividers one in between your lower Y-pipe and one mid exhaust manifold. TO seperate your air flow from both turbos into the same direction.
The SEQ. turbo is the best concept ever HOWEVER this design is horrible. To cut a long story short you got two turbos forcing air agaist each other. thats why you get all kind of spikes and motor blowouts.
THE FIX. $$ have a welding guru weld dividers one in between your lower Y-pipe and one mid exhaust manifold. TO seperate your air flow from both turbos into the same direction.

