Kevin Wyum's IC pipe test fitting - airpump friendly
#1
Kevin Wyum's IC pipe test fitting - airpump friendly
Kevin stopped by to test fit his 'airpump friendly' IC pipe on my street car.
Here are pics I took:
some of the pipe:
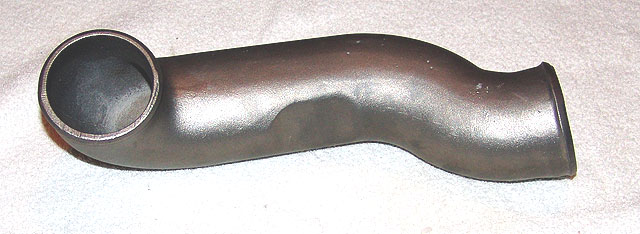
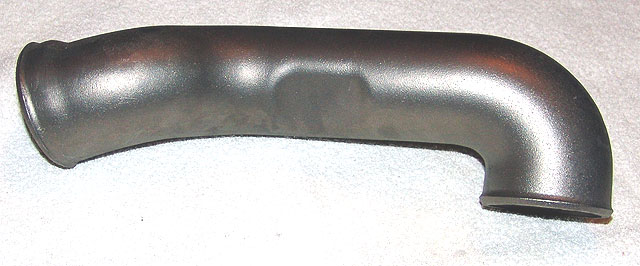
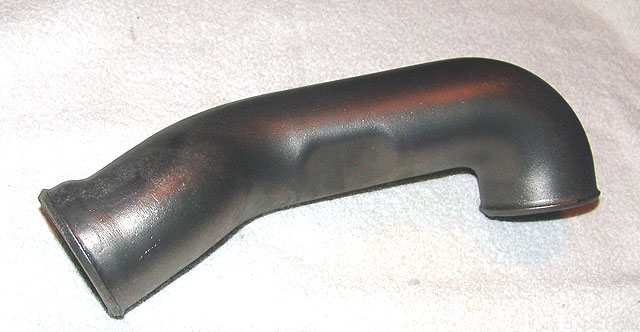
some of it on my car during the test fit:
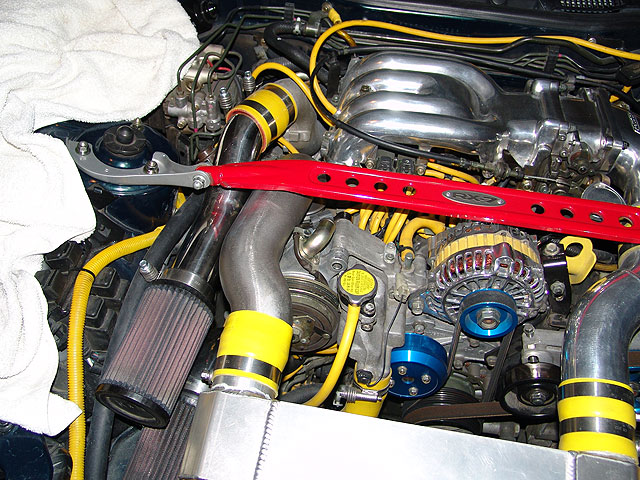
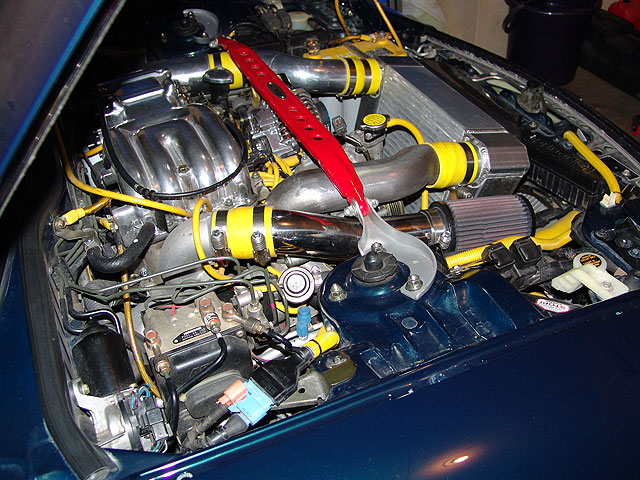
some shots of airpump clearance and tower bar clearance:
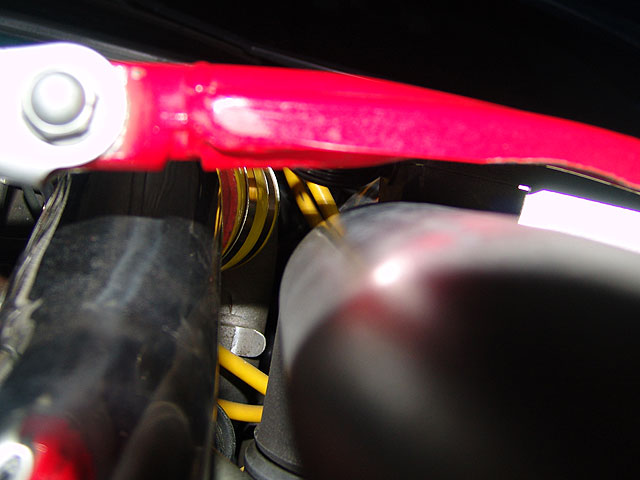
Here are pics I took:
some of the pipe:
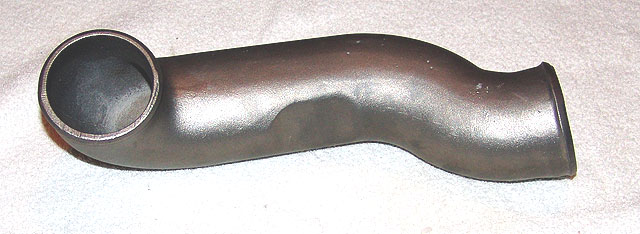
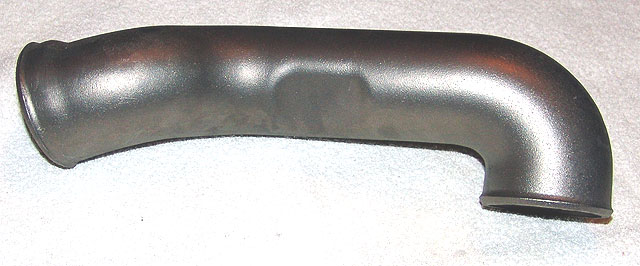
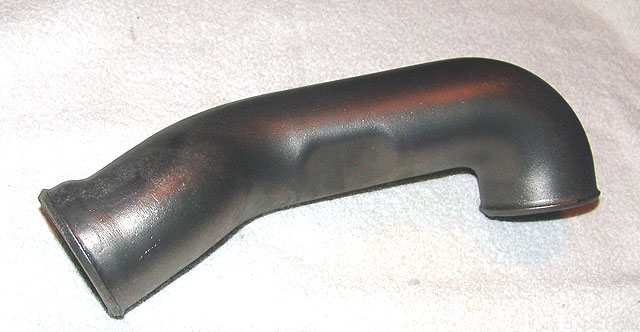
some of it on my car during the test fit:
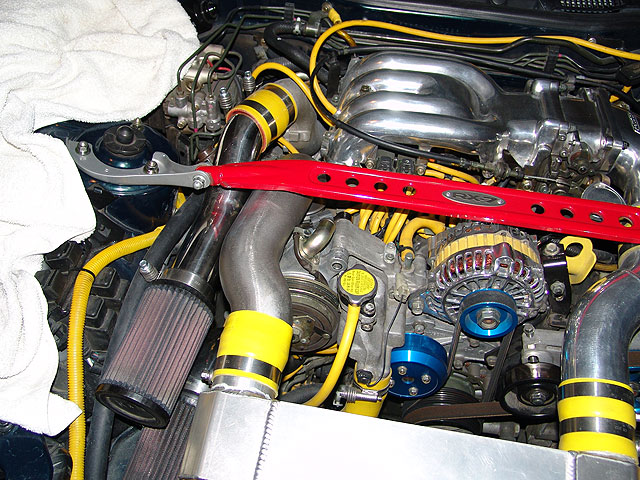
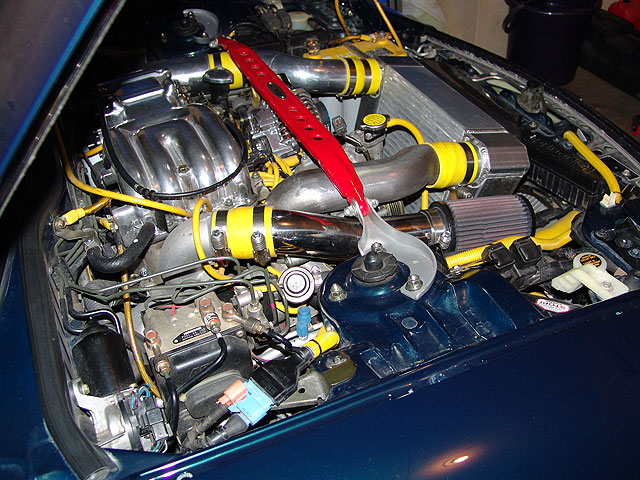
some shots of airpump clearance and tower bar clearance:
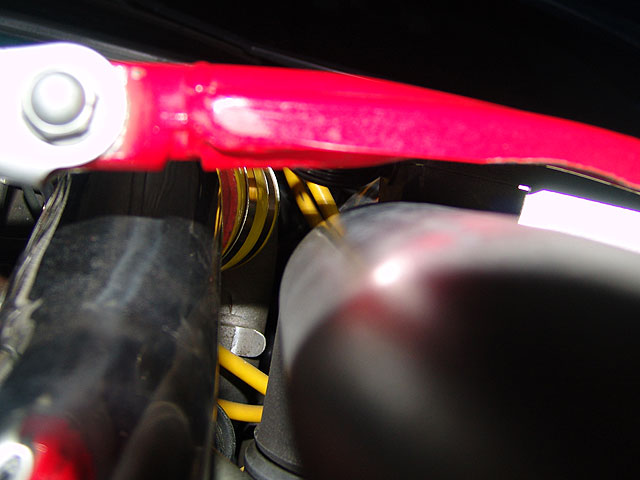
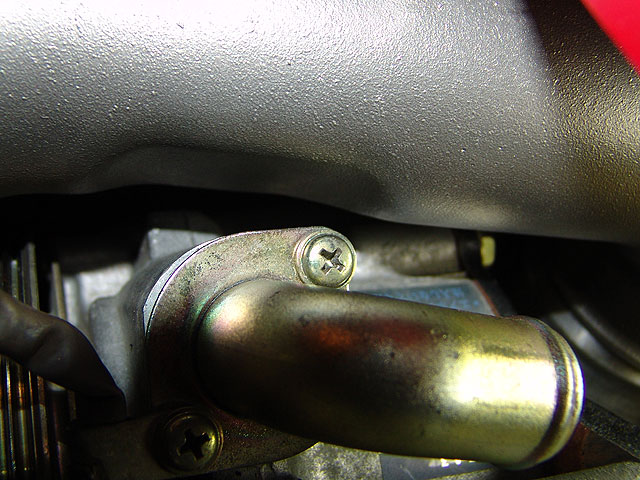
#4
The M2 Intercooler is actually the Kevin Wyum ASP Racing IC : ). I had a contract with M2 to let them make copies of both of my intercoolers for a number of years. They wanted to use their shop name which was fine with me.
We made this pipe to be pretty universal, not just for my IC's. Of course the first function was for it to fit with my IC's with the airpump in place and to clear the OEM strut tower brace without scraping etc. The unfortunate reality before was that the stock setup uses 2-3/4" tube diameters and a rule of thumb is that you cannot bend tubing on a sharper radius than its diameter. Because of that you could never make a tubing based pipe that didn't cut real close to hitting the strut tower bar, hood etc. because the bend coming out of the turbo Y pipe was too sharp to make with tubing, hence all this effort of a new cast pipe.
The universal part comes when we talk about people using front mounts or a lot of other IC's, on the twins, being forced to use the OEM flat plastic tube that goes around the inside of the airpump and forces a lot of extra tubing bends, which is not a desirable thing. They could now use this pipe to make a much straighter path to their IC while still having good clearance for the brace and hood etc. The best way to think of it is to imagine routing your IC piping from where my ICs start at with a coupler. It should be a much better flow path as I mentioned. Well the pictures above should explain it best.
Thanks Damian for posting those. I'm not nearly as web handy and sure admire his fancy camera : ).
Kevin T. Wyum
We made this pipe to be pretty universal, not just for my IC's. Of course the first function was for it to fit with my IC's with the airpump in place and to clear the OEM strut tower brace without scraping etc. The unfortunate reality before was that the stock setup uses 2-3/4" tube diameters and a rule of thumb is that you cannot bend tubing on a sharper radius than its diameter. Because of that you could never make a tubing based pipe that didn't cut real close to hitting the strut tower bar, hood etc. because the bend coming out of the turbo Y pipe was too sharp to make with tubing, hence all this effort of a new cast pipe.
The universal part comes when we talk about people using front mounts or a lot of other IC's, on the twins, being forced to use the OEM flat plastic tube that goes around the inside of the airpump and forces a lot of extra tubing bends, which is not a desirable thing. They could now use this pipe to make a much straighter path to their IC while still having good clearance for the brace and hood etc. The best way to think of it is to imagine routing your IC piping from where my ICs start at with a coupler. It should be a much better flow path as I mentioned. Well the pictures above should explain it best.
Thanks Damian for posting those. I'm not nearly as web handy and sure admire his fancy camera : ).
Kevin T. Wyum
#7
Originally Posted by Kento
Looks great, Kevin. I guess good things really do come to those who wait, eh? 
I'm going to have to get my Efini flange welded to that thing, I guess....

I'm going to have to get my Efini flange welded to that thing, I guess....

Trending Topics
#10
Originally Posted by Kevin T. Wyum
The unfortunate reality before was that the stock setup uses 2-3/4" tube diameters and a rule of thumb is that you cannot bend tubing on a sharper radius than its diameter. Because of that you could never make a tubing based pipe that didn't cut real close to hitting the strut tower bar, hood etc. because the bend coming out of the turbo Y pipe was too sharp to make with tubing

#12
it's not the greatest pic and my engine bay could use a good cleaning, but, no, that is a bone stock y-pipe cut down and re-fit with a flange....really cleans up the turbo to IC connection....like I mentioned in another thread, my boost creep went way up after installing this modified y-pipe so I'm confident the flow significantly increased, relative to the half collapsed coupling and "s bend" M2 pipe I ran before
#15
Originally Posted by the_glass_man
Airpump??? 


I'd like to see a similar version for the Enfini pipe for cars without the airpump... althought I'm not sure how many would be interested.
I would love to have a nice quality pipe like that running strait over and into the IC... as it looks now the Greddy FMIC has too many bends because of that thing that I'd like to negate.

~Kris
#16
Kevin That looks great! Congrats on all the hard work.
Damian. I have a Rx7fashion airbox that is similar to the older M2 boxes. This causes a shift of that pipe more toward the drivers side. Do you know anyone who can test fit that pipe in a car with a airbox?
Damian. I have a Rx7fashion airbox that is similar to the older M2 boxes. This causes a shift of that pipe more toward the drivers side. Do you know anyone who can test fit that pipe in a car with a airbox?
Last edited by 7racer; 12-11-04 at 12:25 PM.
#19
Originally Posted by scratchjunkie
wow, where can i order one?
Kevin T. Wyum
#21
It's not a flimsy piece by any means. Damian's first reaction was, "This thing could be a weapon." It's along the lines of the stock cast parts maybe a little tougher. The foundry didn't want to be too thin because of pitting during the casting process and possible leaks since it's for a pressurized application. I was definately surprised how strong it is but don't have a small scale for this kind of thing, I'd guess a couple pounds.
Kevin T. Wyum
Kevin T. Wyum
#22
Originally Posted by Kevin T. Wyum
It's not a flimsy piece by any means. Damian's first reaction was, "This thing could be a weapon." It's along the lines of the stock cast parts maybe a little tougher. The foundry didn't want to be too thin because of pitting during the casting process and possible leaks since it's for a pressurized application. I was definately surprised how strong it is but don't have a small scale for this kind of thing, I'd guess a couple pounds.
Kevin T. Wyum
Kevin T. Wyum
