Fuel system upgrade how to - write up for KGparts kit.
#26
Originally Posted by damian
glad to help, be sure to follow all the other posts in here as some had great suggestions to improve the setup. according to the previous owners post, my track car uses a RP Hi Flow fuel pump:
https://www.rx7club.com/showthread.p...hreadid=211166
https://www.rx7club.com/showthread.p...hreadid=211166
If you do decide to add an FPD, you need two since you are running the lines in parallel.
This is exactly how I'm building my fuel lines right now, but no plan to run any FPD.
As for the FJO injector driver, well that looks like a really well thought out piece; another thing to add to the list!

#28
Originally Posted by damian
Ok, so here is my attempt at a comprehensive fuel system upgrade writeup. I need to thank Keith, Steve, and Shawn for helping me a lot in this process.
This writeup will be based on upgrading the primary and secondary rails and injectors, as well as SS braided line for everything in the engine bay to the firewall. My upgrade uses a kit from KGParts.
First lets start by looking at my system before the upgrade, as you will see I already had an aftermarket FPR and the fuel filter was moved up here from the rear.
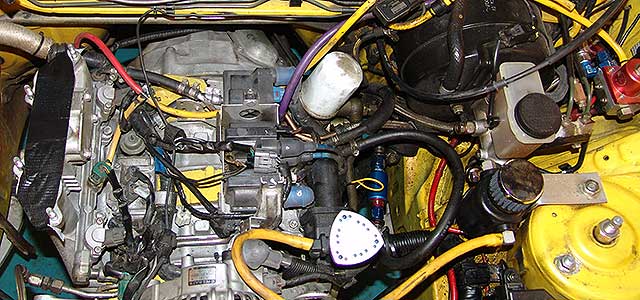
Here is a drawing to better see how it was:
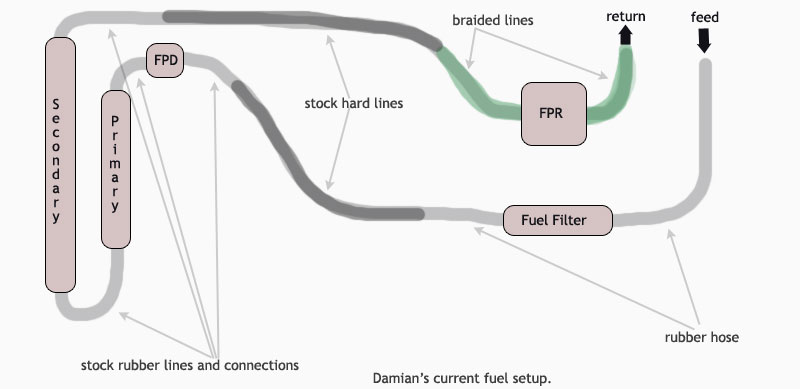
Here is a picture of the new kit from KGParts:
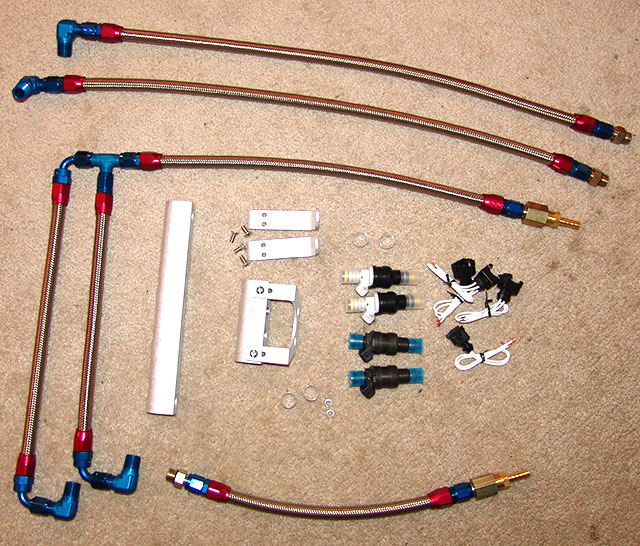
The new kit runs a bit differently, the rails are not in series like the stock system, they are in parallel, so they both get their own feed from the main feed line and they get their own return to the FPR.
Here is a drawing of how I planned to run my new setup:
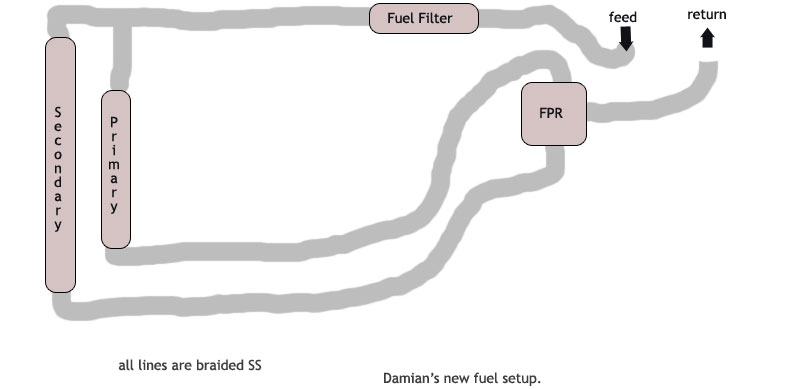
Summary Of Install
1) relieve gas pressure (search forums, there is plenty of info on how to do this)
2) remove all old rails/injectors/lines
keep some towels around as there will be gas in the rails/lines and you want to place towels under these areas before disconnecting. Not a big deal as it evaporates fast anyway. I let a lot dump around and it was gone in minutes.
3) before installing anything, lay it out on the engine where its supposed to go, including the lines. This helps you plan if you need to change line lengths or use different fittings to make the lines go where you want them without kinking them up. This step saved me a lot of trouble in determining the FPR placement and fuel filter placement and what was needed to make both happen correctly.
4) Washed out the rails and checked all the holes for 'hangnails' that could be filed off. You dont want 'dirty rails' going in there :-)
5) Put the sleeves on the injectors, according to the info I got it was the shorter sleeves on the secondaries and the longer ones on the primaries. I also used a bit of motor oil to lube the injector 0-rings.
6) On the primaries, remove the stock diffuser and follow the process outlined below on using them as a seal for the injectors. on the secondaries pull out the old seal and diffuser. The injector install quirks are detailed below. I had to use things that looked like dentist tools in order to get the diffusers out without destroying them. YOU WANT TO KEEP THEM INTACT, YOU WILL END UP USING PART OF THEM.
7) Install the rails, lines, and whatever else you upgraded (fpr, gauge, et)
8) Setup your electrical connectors with the resistors, clip the old connectors and solder the new ones in. Apparently the resistor can go on either side and the connectors wires can go on either wire of the stock connector. Just keep track of what connector goes to what injector.
Those are the basics, here are pictures and details of certain aspects of the install.
This writeup will be based on upgrading the primary and secondary rails and injectors, as well as SS braided line for everything in the engine bay to the firewall. My upgrade uses a kit from KGParts.
First lets start by looking at my system before the upgrade, as you will see I already had an aftermarket FPR and the fuel filter was moved up here from the rear.
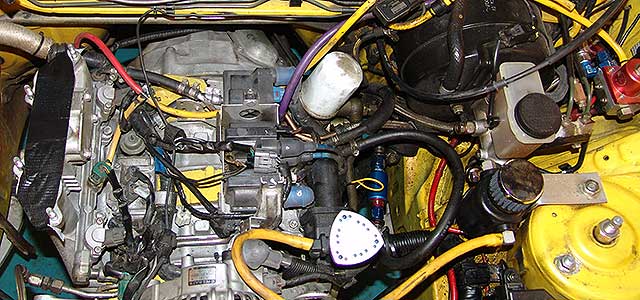
Here is a drawing to better see how it was:
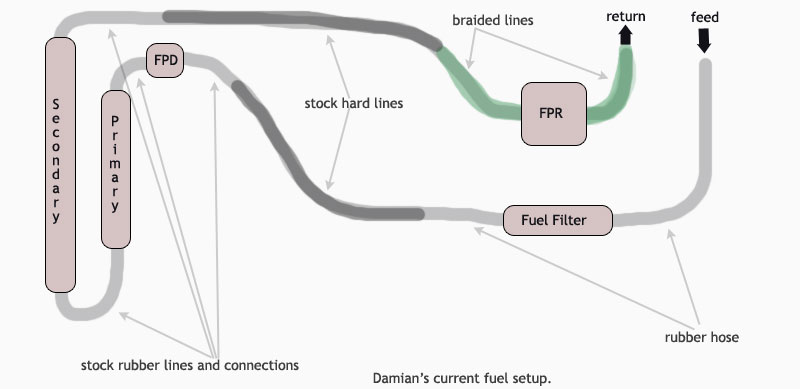
Here is a picture of the new kit from KGParts:
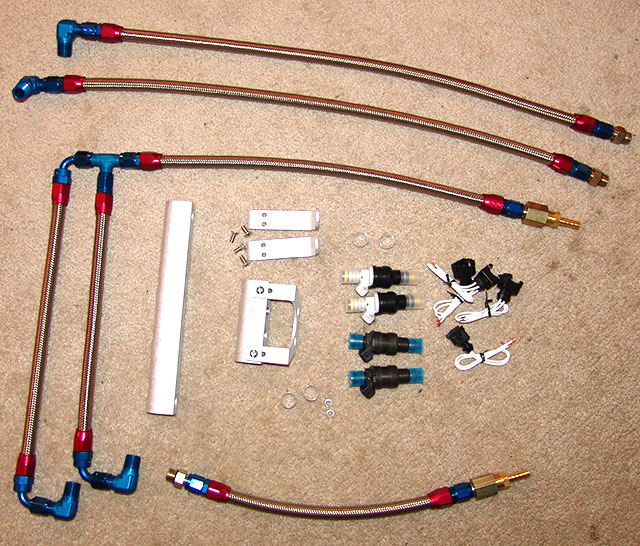
The new kit runs a bit differently, the rails are not in series like the stock system, they are in parallel, so they both get their own feed from the main feed line and they get their own return to the FPR.
Here is a drawing of how I planned to run my new setup:
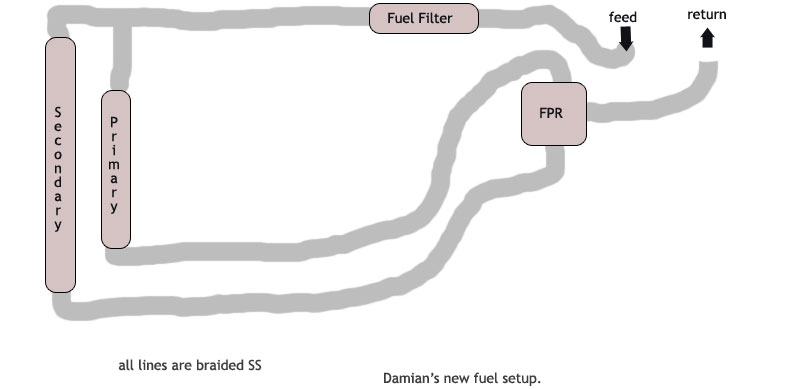
Summary Of Install
1) relieve gas pressure (search forums, there is plenty of info on how to do this)
2) remove all old rails/injectors/lines
keep some towels around as there will be gas in the rails/lines and you want to place towels under these areas before disconnecting. Not a big deal as it evaporates fast anyway. I let a lot dump around and it was gone in minutes.
3) before installing anything, lay it out on the engine where its supposed to go, including the lines. This helps you plan if you need to change line lengths or use different fittings to make the lines go where you want them without kinking them up. This step saved me a lot of trouble in determining the FPR placement and fuel filter placement and what was needed to make both happen correctly.
4) Washed out the rails and checked all the holes for 'hangnails' that could be filed off. You dont want 'dirty rails' going in there :-)
5) Put the sleeves on the injectors, according to the info I got it was the shorter sleeves on the secondaries and the longer ones on the primaries. I also used a bit of motor oil to lube the injector 0-rings.
6) On the primaries, remove the stock diffuser and follow the process outlined below on using them as a seal for the injectors. on the secondaries pull out the old seal and diffuser. The injector install quirks are detailed below. I had to use things that looked like dentist tools in order to get the diffusers out without destroying them. YOU WANT TO KEEP THEM INTACT, YOU WILL END UP USING PART OF THEM.
7) Install the rails, lines, and whatever else you upgraded (fpr, gauge, et)
8) Setup your electrical connectors with the resistors, clip the old connectors and solder the new ones in. Apparently the resistor can go on either side and the connectors wires can go on either wire of the stock connector. Just keep track of what connector goes to what injector.
Those are the basics, here are pictures and details of certain aspects of the install.
#29
Most likely he used the econo fit ends.
http://www.jegs.com/cgi-bin/ncommerc...60&prmenbr=361
Thats what I'm using.
http://www.jegs.com/cgi-bin/ncommerc...60&prmenbr=361
Thats what I'm using.
#31
>>According to Aeromotive, the 1000 (looks like that is what you have) has built in dampening effects.
yup, that is what I understood too, thus the removal of the stock FPD.
yup, that is what I understood too, thus the removal of the stock FPD.
#32
>>How did you connect the braided hose to the hard pipes coming from the gas tank? Pics?
they dont go all the way to the gas tank, they stop at the firewall and connect to the stock lines that goto the tank. I just slipped them over the hardlines and used 2 clamps on each line.
they dont go all the way to the gas tank, they stop at the firewall and connect to the stock lines that goto the tank. I just slipped them over the hardlines and used 2 clamps on each line.
#33
Originally Posted by Scrub
Most likely he used the econo fit ends.
http://www.jegs.com/cgi-bin/ncommerc...60&prmenbr=361
Thats what I'm using.
http://www.jegs.com/cgi-bin/ncommerc...60&prmenbr=361
Thats what I'm using.
i did think about getting these, but then decided you cant really see those connections anyway so I went with just the braided line with 2 standard worm drive clamps over each one.
#35
Nice setup, Damian. I ran my fuel system with KG rails in a parallel setup much like that last spring. I have pictures somewhere, but your's do the thread much more justice. I'm trying to simplify it now because I have too many lines underneath the UIM to allow them to sit loosely. I like the idea of using that plastic spiral wrap stuff. I found some serious chafing marks on some of my parts from where the lines rubbed on other things. I have braided lines on the brake booster connections to the UIM and there's a chunk missing out of my torque brace bar where the aluminum lost a few fights to the stainless. Anyway, nice job on the work. I'll have to save these pictures. For future reference.
Fuel doesn't "slosh" around inside the rails once you've primed the fuel system. Sloshing occurs in the tank, Not in the pressurized system (40-60psi) between the pump and the injectors.
With the KG rails, you bolt your lines right on with AN fittings. The stock fuel rails are the only ones really designed to use those types of FPD's.
Parallel vs Series- no real advantage to it since the system is all dependent upon the same device- FPR.
Originally Posted by Scrub
you also may want to consider a fuel pusation damper...I just got one from marren for like $114, it's an aftermarket one.
http://www.injector.com/fueldampers.php
I know a lot of people say you don't need it, but I'd rather not worry about running lean due to fuel getting sloshed around in the rails.
http://www.injector.com/fueldampers.php
I know a lot of people say you don't need it, but I'd rather not worry about running lean due to fuel getting sloshed around in the rails.
With the KG rails, you bolt your lines right on with AN fittings. The stock fuel rails are the only ones really designed to use those types of FPD's.
Parallel vs Series- no real advantage to it since the system is all dependent upon the same device- FPR.
#36
Originally Posted by damian
>>According to Aeromotive, the 1000 (looks like that is what you have) has built in dampening effects.
yup, that is what I understood too, thus the removal of the stock FPD.
yup, that is what I understood too, thus the removal of the stock FPD.
What are you doing about the fuel thermosensor? I'm trying to figure out a way to continue using it so that it provides the right temp for the PFC for correction.
#38
Originally Posted by MakoDHardie
Parallel vs Series- no real advantage to it since the system is all dependent upon the same device- FPR.
With the system in serial, you have have the secondaries coming online and the primary fuel rail is further down the line which will take slightly longer to regain the pressure.
It makes sense when you look at flow; or am I smoking crack?

#39
what sized fitting does the kg parts secondary fuel rail use? I want to replace the stock rubber line coming from the primary rail to the secondary rail with a stainless line.
I know it's not an AN thread type, so I'm not really sure what NPT is uses.
I know it's not an AN thread type, so I'm not really sure what NPT is uses.
Last edited by Scrub; 03-16-05 at 02:57 PM.
#41
Originally Posted by atihun
What are you doing about the fuel thermosensor? I'm trying to figure out a way to continue using it so that it provides the right temp for the PFC for correction.
#42
Originally Posted by damian
nothing, i left it disconected, but now what you mention it i may find a way to tap it back in somewhere, i bet there is some kind of fittign you can put in a line to tap in the sensor. I will have to ask the fuel gods about this. :-)
i"m no fuel God, but..
Just leave it out. The PFC doesn't care and if I remember correctly when you look at the correction tables through the datalogit they are all set to 1.0 anyway..
#43
Originally Posted by NewbernD
i"m no fuel God, but..
Just leave it out. The PFC doesn't care and if I remember correctly when you look at the correction tables through the datalogit they are all set to 1.0 anyway..
Just leave it out. The PFC doesn't care and if I remember correctly when you look at the correction tables through the datalogit they are all set to 1.0 anyway..
#44
Originally Posted by Scrub
what sized fitting does the kg parts secondary fuel rail use? I want to replace the stock rubber line coming from the primary rail to the secondary rail with a stainless line.
I know it's not an AN thread type, so I'm not really sure what NPT is uses.
I know it's not an AN thread type, so I'm not really sure what NPT is uses.
3/8th inch NPT.
#45
in this picture i don't see a heater hose that was punctured in my fd and was leaking all over the place. can you eliminate it. mine had the hard steel line that connected to the firewall on the pass side and the other end attached to the block i guess where the lower radiator hose connected. the steel line was contacting the turbo and melted a hole in it. thanks.
#46
Originally Posted by fd3virgin
in this picture i don't see a heater hose that was punctured in my fd and was leaking all over the place. can you eliminate it. mine had the hard steel line that connected to the firewall on the pass side and the other end attached to the block i guess where the lower radiator hose connected. the steel line was contacting the turbo and melted a hole in it. thanks.
#48
Just wanted to clear up a few things about using resistors and sizing the wattage on the resistors. Before I go any further, injectors worked as an inductance. V=L*di/dt. It is current and frequency dependent more than voltage. The amount of movement and the rate on how fast it moves will be based on the amount of current apply to it (which can be compensated by the injector lag time in most part)
#1. You can get away with it by using smaller resistor or not running any resistors. The only problem is that as your duty cycle goes up, the rise time is higher so that the amount of current to drive the injector will almost be equal to the voltage across the circuit divided by the overall resistance. If the drivers can only support 2Amps continous, you're bound to damage the drivers in the circuit.
#2. 25W vs. 10W resistors, this goes back to the same reasoning for the duty cycle. The resistors rating is usually rate at continous plus approximately of a 15% of design margin. So a 10W resistor should be good to about 12W continous w/o damaging or burning the resistor up. so based on Damian's calculations, You can probably run the 10W resistor as long as the resistance is sized correctly.
I personally prefered some safety margin when it comes to electrical circuit. For those who runs their cars at the track where the car runs WOT continous for a long period of time, I would recommend using the 25W over the 10W.
Also, the resistors that I use are different than the ones that Damian got. It'll work fine but I feel that the leads are too fragile and can break off with enough vibration.
The ones that we use here at the shop are military grade with built-in Aluminum heat sink instead of the ceramic heatsink.
#1. You can get away with it by using smaller resistor or not running any resistors. The only problem is that as your duty cycle goes up, the rise time is higher so that the amount of current to drive the injector will almost be equal to the voltage across the circuit divided by the overall resistance. If the drivers can only support 2Amps continous, you're bound to damage the drivers in the circuit.
#2. 25W vs. 10W resistors, this goes back to the same reasoning for the duty cycle. The resistors rating is usually rate at continous plus approximately of a 15% of design margin. So a 10W resistor should be good to about 12W continous w/o damaging or burning the resistor up. so based on Damian's calculations, You can probably run the 10W resistor as long as the resistance is sized correctly.
I personally prefered some safety margin when it comes to electrical circuit. For those who runs their cars at the track where the car runs WOT continous for a long period of time, I would recommend using the 25W over the 10W.
Also, the resistors that I use are different than the ones that Damian got. It'll work fine but I feel that the leads are too fragile and can break off with enough vibration.
The ones that we use here at the shop are military grade with built-in Aluminum heat sink instead of the ceramic heatsink.
Last edited by pluto; 03-18-05 at 03:23 PM.
#49
good post Steve, thanks.
yeah, i learned about the better resistors after i already installed the ones I purchased, ohh well. I think if i were to go in there to do it again, I would actually get the low imp. injector driver product that was posted earlier in this thread.
http://www.fjoracing.com/index2.htm
I may still try to do this before the car gets tuned, just dunno if i can afford it yet :-)
yeah, i learned about the better resistors after i already installed the ones I purchased, ohh well. I think if i were to go in there to do it again, I would actually get the low imp. injector driver product that was posted earlier in this thread.
http://www.fjoracing.com/index2.htm
I may still try to do this before the car gets tuned, just dunno if i can afford it yet :-)
#50
Originally Posted by damian
Primary Rail and Injectors
Here is what the primary rail and injectors looks like when its installed:
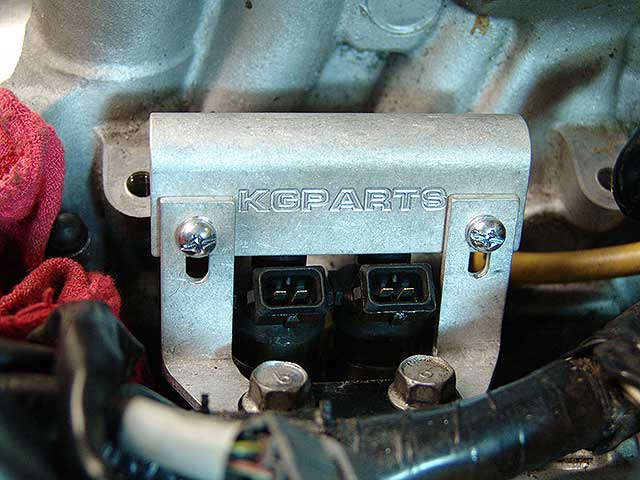
The install is not difficult, but be sure to read below on the seating/sealing of the injectors.
Secondary Rail and Injectors
Here is a picture of a secondary injectors seated:
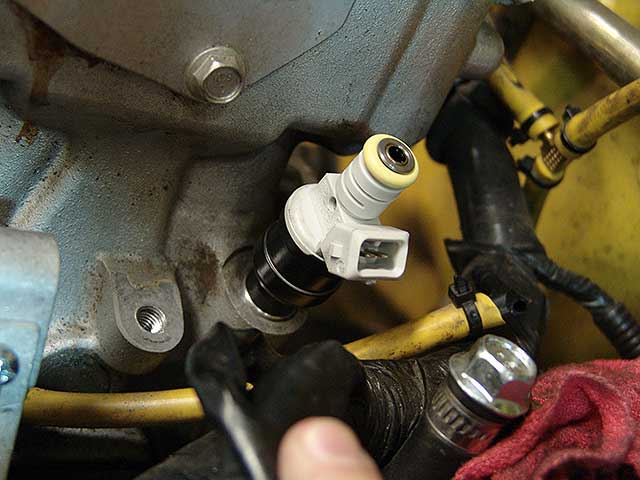
The install is pretty straight forward and the injector should seal fine for the reasons described below.
The Diffusers and Seating/Sealing The Injectors
Ok, there are many ways to go on this but here is what I found and how I ended up dealing with the injectors seating/sealing issues. First of all the sleeves help the injectors seat properly, but it debatable if they actual 'seal' properly by them selves. Some have run only sleeves with no issues, some run sleeves and a small cut of fuel hose up on the injector body to make an external seal. I didnt like either of these options and wanted a seal similar to the stock style. The issue only involves the primary injectors as the secondaries seal fine because the o-ring ends up past the sleeve and it seats against the housing for a great seal.
Here is a picture showing what I mean, the secondary diffuser with sleeve on showing the o-ring protruding out the end:
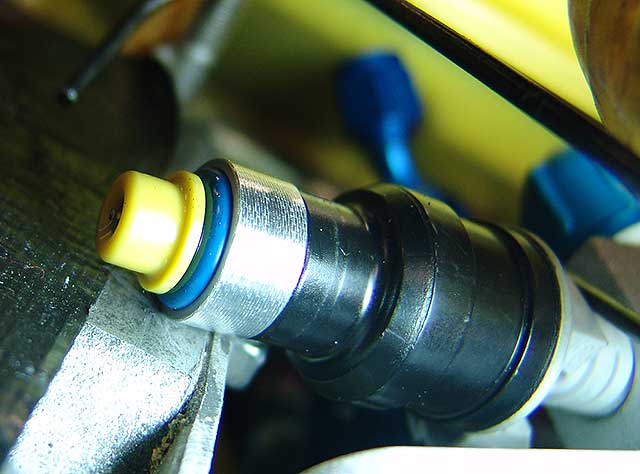
However, the primaries are not so fortunate, the sleeve passes farther than the o-ring, so when installed its the metal of the sleeve against the metal of the housing, with no rubber material sealing them. Now this may work as the sleeves are a very tight fit and it may seal, but I was not feeling good about it.
Here is the primary with the sleeve on, see how the o-ring is totally hidden:
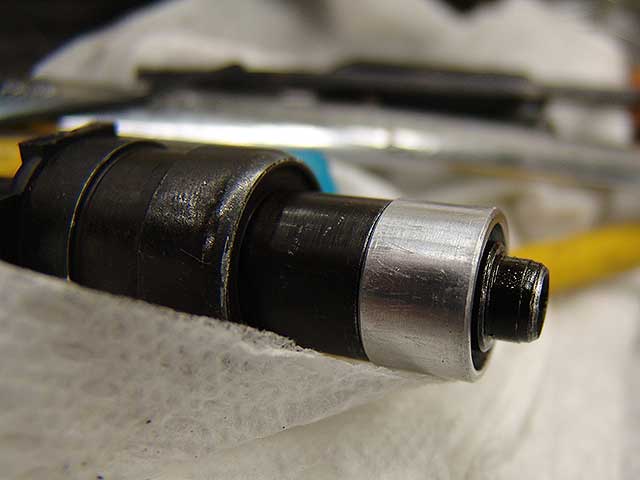
Now, to toss another wrench in this entire deal, is the primary injector holes have a 'notch' at the bottom of them that matches a protrusion on the diffusers that go in there. Its meant to make the diffusers fit in the right way when installed. However it complicates trying to make a good seal with just a sleeve or trying to make your own rubber seal.
Here is a picture of the notches I am referring to:
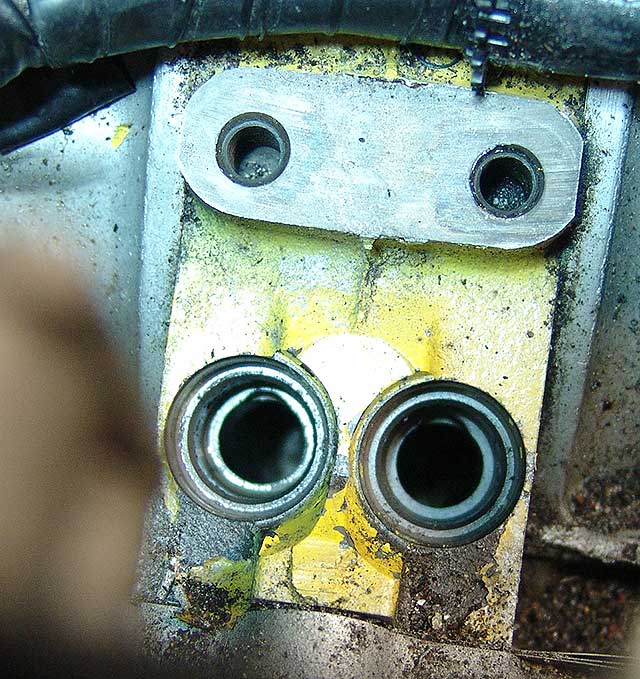
So, to make a long story short, what I did was take the stock primary diffusers and cut the rubber seal that is integrated to the end of it, and then GENTLY bored out the inside of the hole in the diffuser just a bit so that the seal would hit the sleeve after the end of the injector went in the diffuser seal hole. If you do no do this then it will bottom out on the nose of the injector before hitting the sleeve and defeat the purpose as acting as a seal. Be VERY careful when you bose the hole out, it can crack easy an is usually pretty brittle.
Here are the primary diffusers with one modified as mentioned above:
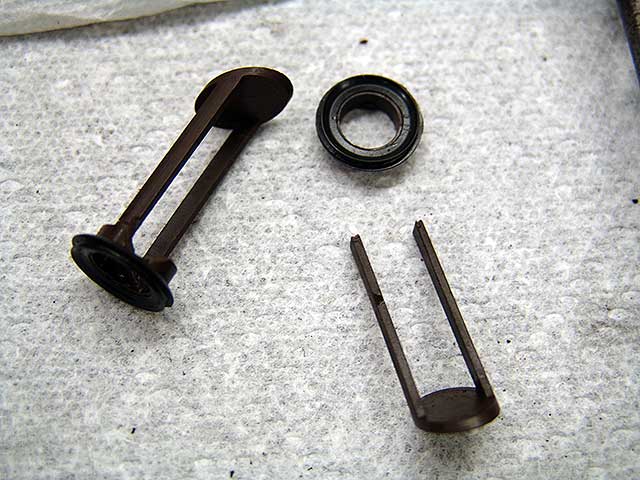
Here is the set with the holes bored out and ready to be used.
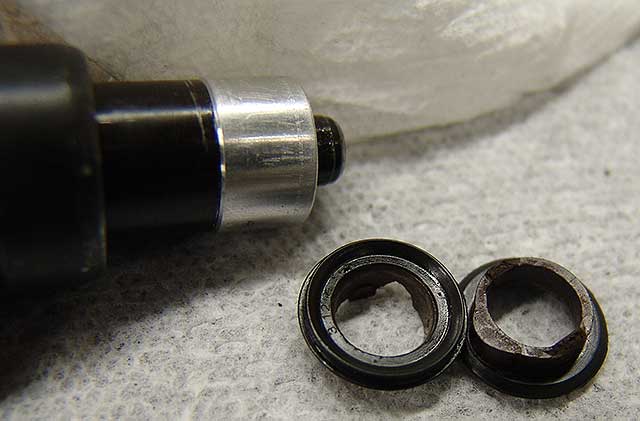
Doing this made a great seal. I started my car for the first time today after installing all this stuff (and all the other winter mods) and it started right up and there was no fuel leaks. Keep in mind I have not run the car in boost yet, I just idled the car, so it has not passed all the tests just yet.
Electrical Connections
There is many posts on if you should or should not use resistors and what ohm resistors, blah blah. Basically here is what I decided to do and why. After getting an education on the actual reasoning behind the resistors it all made sense to me (thanks mainly to steve kan for walking me through the math/physics on all this). From what I understand, the injector drivers on the pfc should not see more that 2 amps. So when you upgrade to the bigger injectors they are most likely lower impedance that the stock injectors. So what you have to do is make sure that there is enough resistance to keep the amps below 2 so you dont run the risk of burning out the injectors drivers. There is a lot of talk about 10 ohm, 6 ohm, and even 4 ohm...but i wanted to know WHY those numbers where being spouted, so after reading a great post by CCarlisi and getting help from steve I now understand. Here is the math (copied from CCarlisi post):
Since Amps=volts/resistance
12v/2.8ohms (bosch 160lb injectors) =4.29 amps without resistors
With 6ohm resistors
12v/2.8+6ohm resistor =1.36 amps
With 10ohm resistors
12v/12.8=.94 amps
Stock injectors
12v/13.8=.87 amps
Now, I measured the resistance on my primaries and they were around 4.5 ohms and the secondaries were 2.8 ohms.
So based on this math I decided to use 3.9 on the primaries and 5.6 on the secondaries. This made them both close to the 8 ohms range in total. Thus keeping my amps under the 2 marker.
And as far as watts go, many use 10 watt but I used 25 watt for the follwing reason (thanks to steve for the math):
12V/6ohm = 2Amps
2Amps * 12V = 24W
To my understanding the higher the watts the better it takes the heat. So I went with 25 to be on the safe side. These resistors were not easy to find locally, but eventually I found 2 online sources for getting these resistors:
http://www.weisd.com/store2/NTERES/NTE25WRESLIST1.html
http://marvac.com/default.aspx (search for resistors)
After I purchased mine I read this thread on some higher end resistors that you may want to use:
https://www.rx7club.com/forum/showth...light=resistor
Here is a pic with them ready to go in:
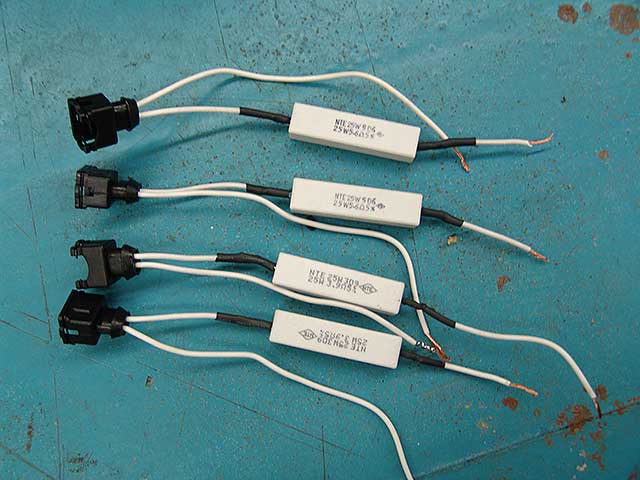
Close up of resistors:
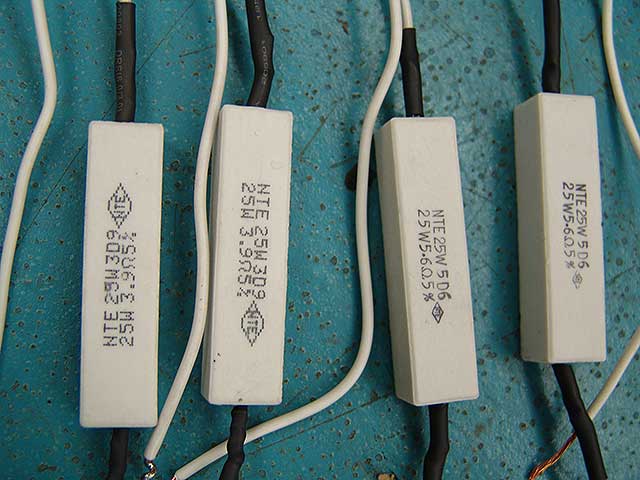
FPR
I wanted this to stay where it was before, in the drivers side corner, so I had to 'edit' some of the braided lines in the kit. Basically I just had to make longer return lines, it was no big deal but braided line is a serious PIA to get fittings on unless you have the right tools and know a good way to do it. It took me a few attempts to get the process of cutting a line and getting a fitting on it, and I will talk about that in the next section. Here is a pic of my FPR and the bracket I made to hold it in place.
[img]http://www.myrx7.com/images/fuel_install_fpr_1.jpg" width="640" height="480" alt="" border="0">
Here is what the primary rail and injectors looks like when its installed:
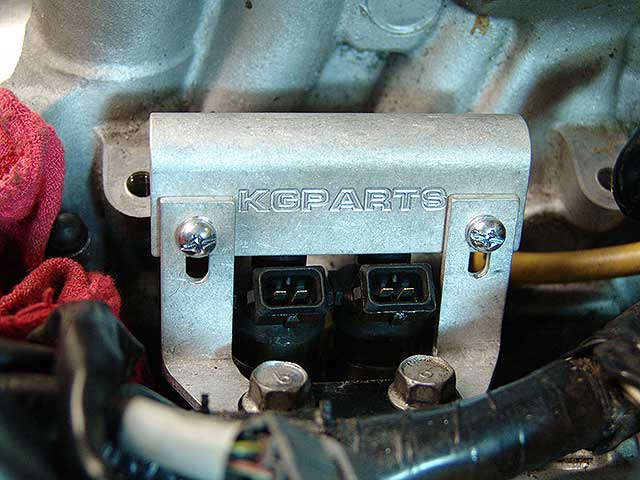
The install is not difficult, but be sure to read below on the seating/sealing of the injectors.
Secondary Rail and Injectors
Here is a picture of a secondary injectors seated:
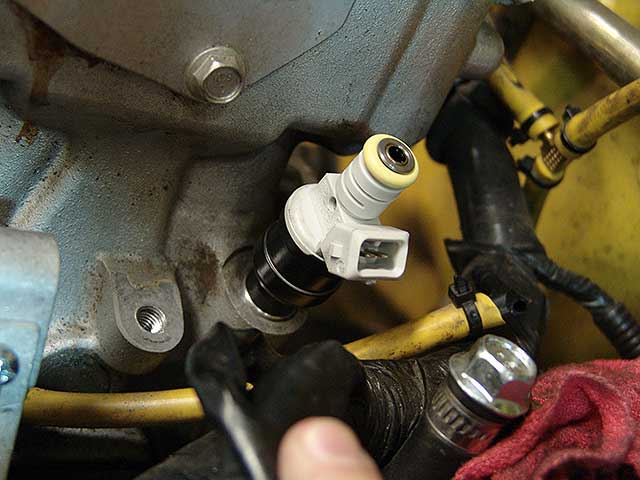
The install is pretty straight forward and the injector should seal fine for the reasons described below.
The Diffusers and Seating/Sealing The Injectors
Ok, there are many ways to go on this but here is what I found and how I ended up dealing with the injectors seating/sealing issues. First of all the sleeves help the injectors seat properly, but it debatable if they actual 'seal' properly by them selves. Some have run only sleeves with no issues, some run sleeves and a small cut of fuel hose up on the injector body to make an external seal. I didnt like either of these options and wanted a seal similar to the stock style. The issue only involves the primary injectors as the secondaries seal fine because the o-ring ends up past the sleeve and it seats against the housing for a great seal.
Here is a picture showing what I mean, the secondary diffuser with sleeve on showing the o-ring protruding out the end:
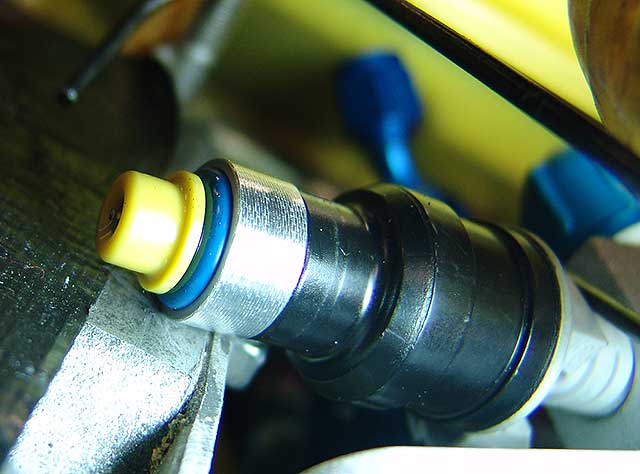
However, the primaries are not so fortunate, the sleeve passes farther than the o-ring, so when installed its the metal of the sleeve against the metal of the housing, with no rubber material sealing them. Now this may work as the sleeves are a very tight fit and it may seal, but I was not feeling good about it.
Here is the primary with the sleeve on, see how the o-ring is totally hidden:
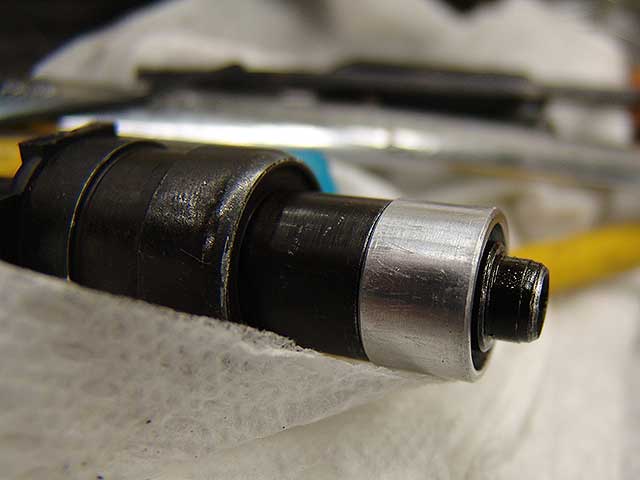
Now, to toss another wrench in this entire deal, is the primary injector holes have a 'notch' at the bottom of them that matches a protrusion on the diffusers that go in there. Its meant to make the diffusers fit in the right way when installed. However it complicates trying to make a good seal with just a sleeve or trying to make your own rubber seal.
Here is a picture of the notches I am referring to:
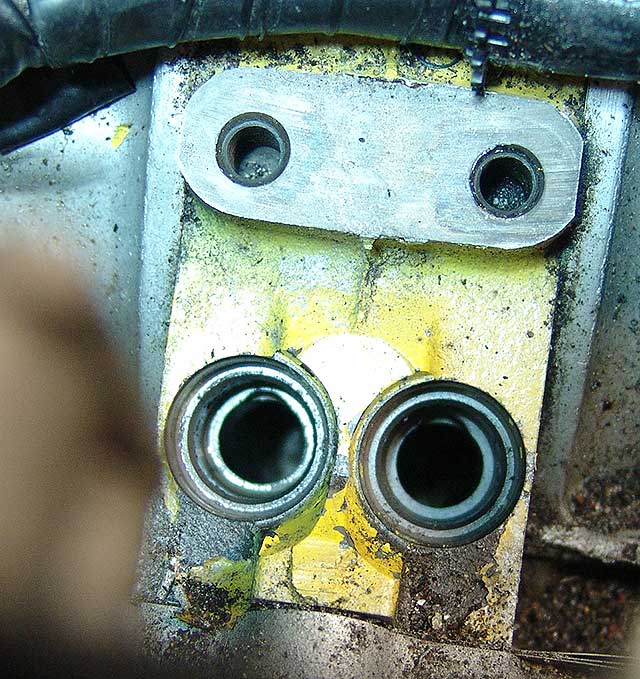
So, to make a long story short, what I did was take the stock primary diffusers and cut the rubber seal that is integrated to the end of it, and then GENTLY bored out the inside of the hole in the diffuser just a bit so that the seal would hit the sleeve after the end of the injector went in the diffuser seal hole. If you do no do this then it will bottom out on the nose of the injector before hitting the sleeve and defeat the purpose as acting as a seal. Be VERY careful when you bose the hole out, it can crack easy an is usually pretty brittle.
Here are the primary diffusers with one modified as mentioned above:
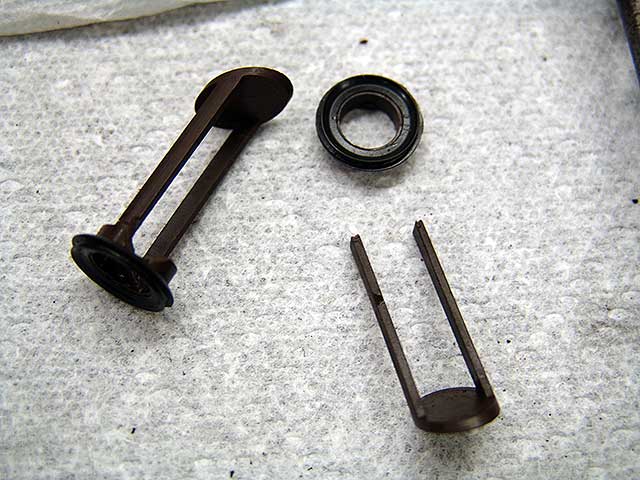
Here is the set with the holes bored out and ready to be used.
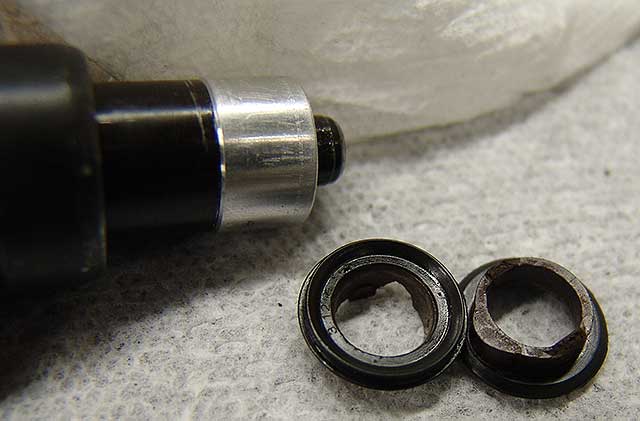
Doing this made a great seal. I started my car for the first time today after installing all this stuff (and all the other winter mods) and it started right up and there was no fuel leaks. Keep in mind I have not run the car in boost yet, I just idled the car, so it has not passed all the tests just yet.
Electrical Connections
There is many posts on if you should or should not use resistors and what ohm resistors, blah blah. Basically here is what I decided to do and why. After getting an education on the actual reasoning behind the resistors it all made sense to me (thanks mainly to steve kan for walking me through the math/physics on all this). From what I understand, the injector drivers on the pfc should not see more that 2 amps. So when you upgrade to the bigger injectors they are most likely lower impedance that the stock injectors. So what you have to do is make sure that there is enough resistance to keep the amps below 2 so you dont run the risk of burning out the injectors drivers. There is a lot of talk about 10 ohm, 6 ohm, and even 4 ohm...but i wanted to know WHY those numbers where being spouted, so after reading a great post by CCarlisi and getting help from steve I now understand. Here is the math (copied from CCarlisi post):
Since Amps=volts/resistance
12v/2.8ohms (bosch 160lb injectors) =4.29 amps without resistors
With 6ohm resistors
12v/2.8+6ohm resistor =1.36 amps
With 10ohm resistors
12v/12.8=.94 amps
Stock injectors
12v/13.8=.87 amps
Now, I measured the resistance on my primaries and they were around 4.5 ohms and the secondaries were 2.8 ohms.
So based on this math I decided to use 3.9 on the primaries and 5.6 on the secondaries. This made them both close to the 8 ohms range in total. Thus keeping my amps under the 2 marker.
And as far as watts go, many use 10 watt but I used 25 watt for the follwing reason (thanks to steve for the math):
12V/6ohm = 2Amps
2Amps * 12V = 24W
To my understanding the higher the watts the better it takes the heat. So I went with 25 to be on the safe side. These resistors were not easy to find locally, but eventually I found 2 online sources for getting these resistors:
http://www.weisd.com/store2/NTERES/NTE25WRESLIST1.html
http://marvac.com/default.aspx (search for resistors)
After I purchased mine I read this thread on some higher end resistors that you may want to use:
https://www.rx7club.com/forum/showth...light=resistor
Here is a pic with them ready to go in:
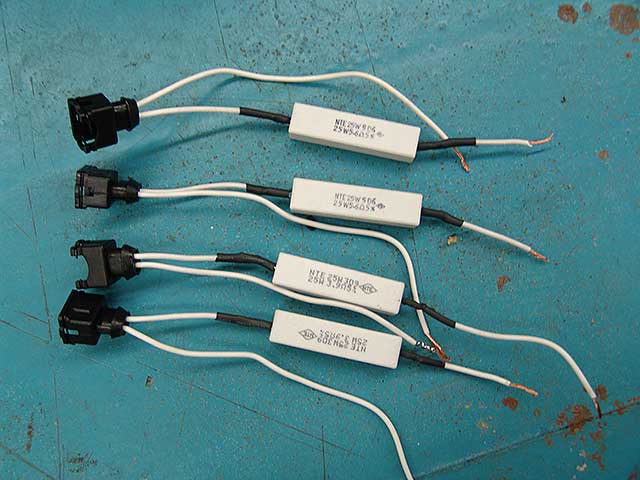
Close up of resistors:
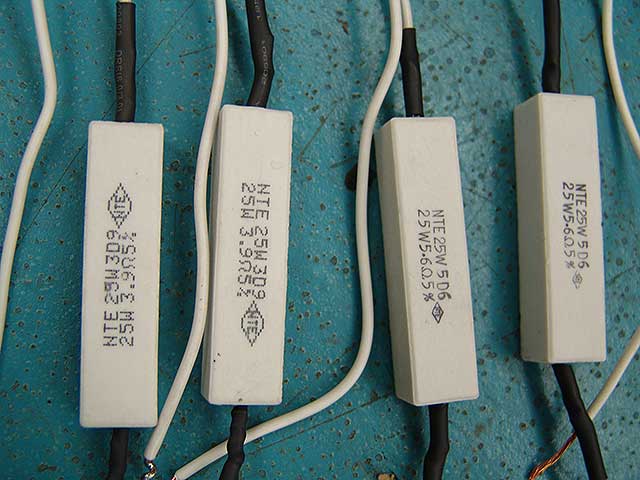
FPR
I wanted this to stay where it was before, in the drivers side corner, so I had to 'edit' some of the braided lines in the kit. Basically I just had to make longer return lines, it was no big deal but braided line is a serious PIA to get fittings on unless you have the right tools and know a good way to do it. It took me a few attempts to get the process of cutting a line and getting a fitting on it, and I will talk about that in the next section. Here is a pic of my FPR and the bracket I made to hold it in place.
[img]http://www.myrx7.com/images/fuel_install_fpr_1.jpg" width="640" height="480" alt="" border="0">
With 2 pumps in stock tank are you planning to run ?