Electric water pump fail safe system
#26
Originally Posted by Black91n/a
I did a quick search on Google and came up with some sources and information for large PVC check valves. So we at least know that they exist, but finding a local source could be more difficult.
http://www.plastomatic.com/ckscatalog.pdf
http://www.plumbingstore.com/pvccheck.html
The first link includes some technical specs, and for a flow rate of about 55GPM there's a pressure drop of only about 2.1psi for the 2" valve. For a 1.5" valve the pressure drop would be about 2.8psi.
http://www.plastomatic.com/ckscatalog.pdf
http://www.plumbingstore.com/pvccheck.html
The first link includes some technical specs, and for a flow rate of about 55GPM there's a pressure drop of only about 2.1psi for the 2" valve. For a 1.5" valve the pressure drop would be about 2.8psi.
Originally Posted by Black91n/a
As for fitting them it should be relatively easy, just insert a short length of PVC pipe and clamp a hose to it. One potential problem I see is the size of all the extra plumbing required to run a parallel twin pump setup like I've proposed. There may not be room for all of it.
For people that have limited room, you can try mounting the two EWP's on top of each other, rather than side by side. Although I have the room, I might still do this just in case I want more left over room for other items.
-Alex
#27
With the check valves, there may be something available in 1.25", but if not, a reducer may be the answer, or you could just make your own valve. I've seen the pictures of your other work and I must say, it looks top notch. You must be wading through a sea of aluminum chips at the end of some days.
For the backflow (flow going from the on pump backwards through the off pump) without such a valve, it will most likely exist, but the rate at which it exists is dependant on the pressure required to flow coolant through the off pump and the pressure drop across the entire cooling loop. For it to not exist the pressure required to force flow through an off pump must be more than the pressure drop across the entire coolant system. I'd be willing to bet that the pressure drop across the cooling system is significantly larger than what's required to force fluid through the off pump. That would mean that a significant portion of the coolant isn't reaching the coolant system at all. With both on, there'll be no problems with backflow. I'd probably run them no matter what, as it's good for piece of mind knowing that all the coolant being pumped is getting to the cooling system.
For parallel fuel pumps there may be some backflow if only one's on, but it may not be enough to worry about, or the pumps may require more pressure to flow when off than they generate when on. Fuel pumps are likely to be quite different internally, as they're a much higher pressure pump, so they'd have very different backflow characteristics.
You may want to contact Meziere to ask them if they think that backflow would be a problem. They may even have some flow vs pressure drop data for a pump that's off. That would at least give a more experianced oppinion on this matter.
For the backflow (flow going from the on pump backwards through the off pump) without such a valve, it will most likely exist, but the rate at which it exists is dependant on the pressure required to flow coolant through the off pump and the pressure drop across the entire cooling loop. For it to not exist the pressure required to force flow through an off pump must be more than the pressure drop across the entire coolant system. I'd be willing to bet that the pressure drop across the cooling system is significantly larger than what's required to force fluid through the off pump. That would mean that a significant portion of the coolant isn't reaching the coolant system at all. With both on, there'll be no problems with backflow. I'd probably run them no matter what, as it's good for piece of mind knowing that all the coolant being pumped is getting to the cooling system.
For parallel fuel pumps there may be some backflow if only one's on, but it may not be enough to worry about, or the pumps may require more pressure to flow when off than they generate when on. Fuel pumps are likely to be quite different internally, as they're a much higher pressure pump, so they'd have very different backflow characteristics.
You may want to contact Meziere to ask them if they think that backflow would be a problem. They may even have some flow vs pressure drop data for a pump that's off. That would at least give a more experianced oppinion on this matter.
#28
parden me for butting in. I run an elect water pump on my race car, the elect pump is much better at cooling as it does not cavatate. if you noticed the electric water pump adapter plate is designed for #8 an. my suggestion is use an fittings and plug in connector and have spare in the trunk! it would take no time to change. I also like the ability to run pump and fan to cool motor with out it running. some times simple is safer. eather way i hope it goes well.
#29
Originally Posted by Busted7
parden me for butting in. I run an elect water pump on my race car, the elect pump is much better at cooling as it does not cavatate. if you noticed the electric water pump adapter plate is designed for #8 an. my suggestion is use an fittings and plug in connector and have spare in the trunk! it would take no time to change. I also like the ability to run pump and fan to cool motor with out it running. some times simple is safer. eather way i hope it goes well.
I'm about to put in my new rebuilt/ported 13brew engine and now, instead of putting the stock water pump, I'm now going ahead and put an EWP. This way when I'm ready ready to put 20B, I'll be half way done.
Alex,
Thanks for the pic of the check valve. I figure it was something like that.. I'm still thinking how it could be incorporated and if its really necessary..
I've also emailed Meizere about running 2 pumps and back flow issues. I haven't heard back since sending it yesterday morning.
PHIL
Last edited by Herblenny; 04-26-06 at 11:26 PM.
#31
I run a meziere water pump, the kind that bolts directly to a flange you weld onto the rad.
I run -16 lines
the fillerneck is on the radiator, FC style. It wasnt hard to retrofit the KOYO to do this.
AST is eliminated.
There is no thermostat in my system.
The alternator is mounted using a custom bracket system, in the stockish location. I may run it in the AC compressor location later as it will look much cleaner and leave room for a custom intake manifold with plentium.
My water temps rarely go above 90 C when BEATING on the car. Fans are set to turn on at 80 C.
I got two pumps by accidnet (thanks summit
) and am very greatful, as EWP's have a reputation for pooping out. I have not had a problem with mine, and have been around numerous other racers using the meziere pumps with zero problems, so if mine ever does go at least I have a spare one sitting around.
Overall it was worth the hastle, but if you dont have some decent fabrication resources (specifically welding AL) at your disposal it may become more pain then it is worth.
If the pump fails I will know just by monitoring temps.
In the future when I get my PCS digital dash, I will have the dash read the coolant sensor in the block and flash a warning light when it reaches a certain temp (110, or whatever is slightly out of operating range) so i can verify that the pump is running, etc.
I run -16 lines
the fillerneck is on the radiator, FC style. It wasnt hard to retrofit the KOYO to do this.
AST is eliminated.
There is no thermostat in my system.
The alternator is mounted using a custom bracket system, in the stockish location. I may run it in the AC compressor location later as it will look much cleaner and leave room for a custom intake manifold with plentium.
My water temps rarely go above 90 C when BEATING on the car. Fans are set to turn on at 80 C.
I got two pumps by accidnet (thanks summit

Overall it was worth the hastle, but if you dont have some decent fabrication resources (specifically welding AL) at your disposal it may become more pain then it is worth.
If the pump fails I will know just by monitoring temps.
In the future when I get my PCS digital dash, I will have the dash read the coolant sensor in the block and flash a warning light when it reaches a certain temp (110, or whatever is slightly out of operating range) so i can verify that the pump is running, etc.
Last edited by rfreeman27; 04-30-06 at 03:15 AM.
#32
Originally Posted by herblenny
Alex,
What are you doing about thermostat, filler neck, AST, and what radiator are you using?
How about the alternator?
PHIL
What are you doing about thermostat, filler neck, AST, and what radiator are you using?
How about the alternator?
PHIL

2. Filler neck - I'll be making a bracket to bolt to the motor where the factory w/p was, and I'll have two tapped holes on the plate for the lines to run to/from the EWP/radiator. I'll then make a filler neck that will screw into one of the tapped holes, and have a tapped hole on the other side of the filler neck for a fitting, so I can run a line to the EWP. All lines will be SS braided.
3. AST - Probably won't run one.
4. Radiator - I plan on having one custom built by Ron Davis.
5. The plate I was speaking of above will have two mounting points for the alt. However, it'll push the alt. closer to the front of the car, so I can use the front part of the main pulley. This will allow more clearance for my custom intake manifold, and i'll only have to run one belt for my alt., P/S, & A/C. The alt. will be solid mounted, and I'll be using the factory belt tensioner that was originally for just the P/S, & A/C.
-Alex
Last edited by TT_Rex_7; 06-08-06 at 05:00 AM.
#33
shouldn't need a t-stat...as the pump turn on point will start the flow in/out of the block. Or are you talking about an temp sender type t-stat to turn the pump on?
we mounted the MoTeC sensor in the bottom of the remote filler neck, the MoTeC will turn on the pump...then at higher temp the fans.
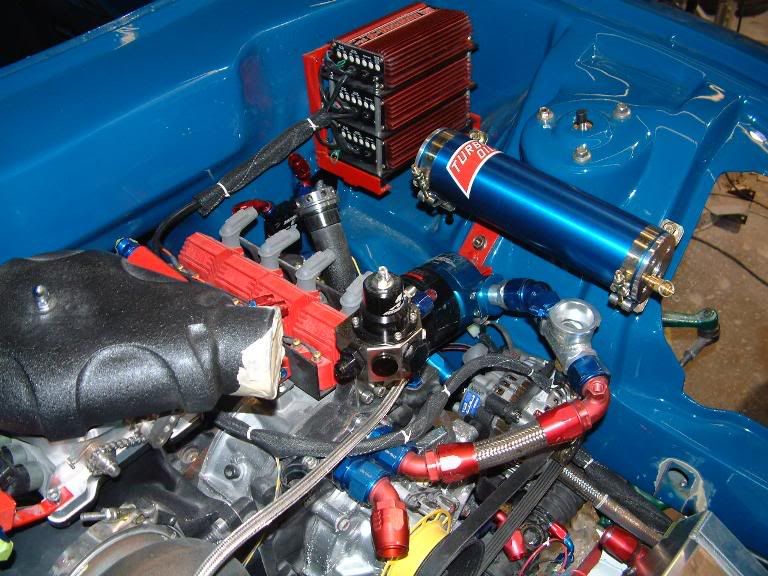
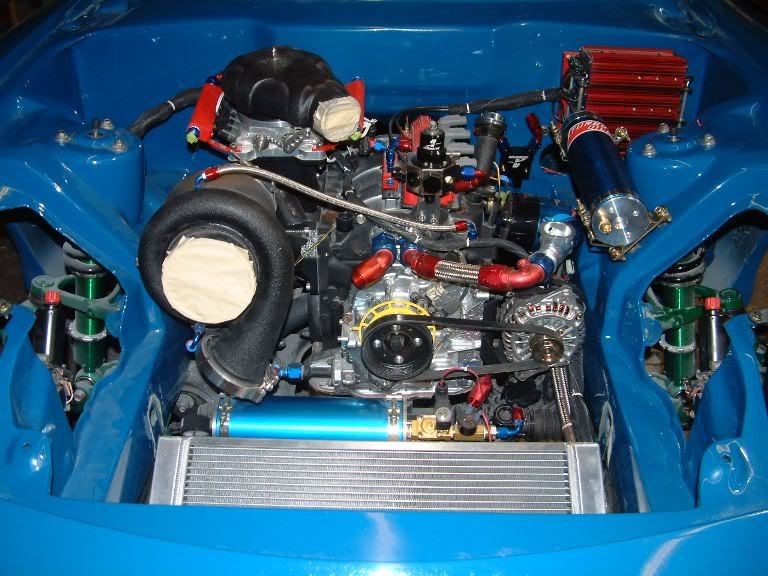
Using the temp sender on the rear iron, we should be able to calculate/compensate what the MoTeC will read in the filler neck, and turn the pump on accordingly.
we mounted the MoTeC sensor in the bottom of the remote filler neck, the MoTeC will turn on the pump...then at higher temp the fans.
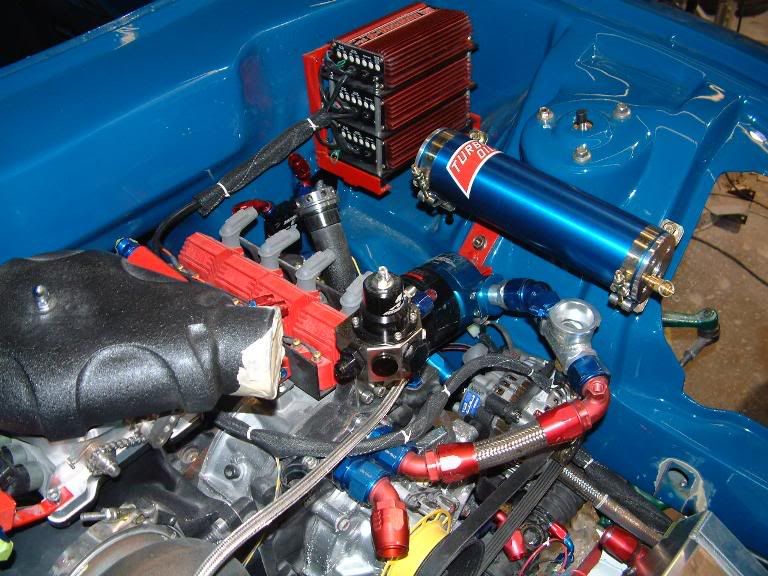
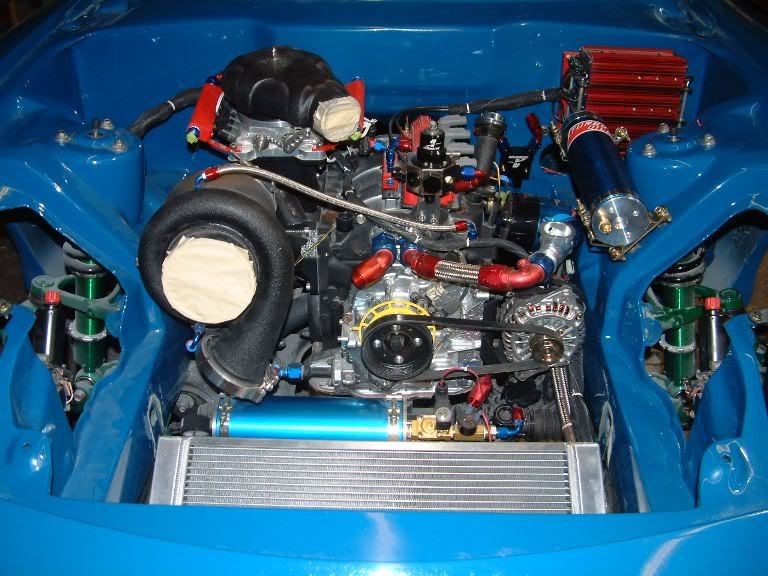
Using the temp sender on the rear iron, we should be able to calculate/compensate what the MoTeC will read in the filler neck, and turn the pump on accordingly.
#34
Do a quality install of a single quality electric pump and nothing else. All this fail-safe business is overcomplicating things and useless anyway. Your stock waterpump was driven by a belt and it had no fail safe. If the belt broke you lost all your cooling and you notice a failure because the car gets hot and you shut it down. Same with an electric pump. If you have such little faith in the electric pump don't install it in the first place! That's folly.
Last edited by DamonB; 06-08-06 at 10:57 AM.
Thread
Thread Starter
Forum
Replies
Last Post
sherff
Adaptronic Engine Mgmt - AUS
9
02-24-19 01:09 PM