Stewie says "It's a Boy!" - I say, it's an FC 20B!! We're both right though =)
#76
Hey mate - thanks for the kind words =)
Seriously, I was thinking e85 was so great that it negated the need to go LPG. Lately I have been reconsidering the LPG scenario; but I'm not "there" yet. I'm going to get the emissions test done on metho - as I think it's the only way to pass it on liquid fuel. What you touched on re efficient idling is so true and also the tip of the 20B iceberg. They are a *very* dirty engine. I enabled the 14.4 afr closed loop in the Wolf V500 up to 40% load and watched how it ran... Um... Well it wouldn't idle for a start! The 20B with no porting is dirty. The 20B with mild porting is *very* dirty, and the logic continues... It's simply this: It WANTS to run rich... So yeah... It's a challange.
After it passes engineering (only emissions is holding it back now), I will be sitting down with a dyno and tuner and doing the water injection. I'll keep running 98ron, but I will be able to do a leaner tune with the water injection...
This project has been a challange and a half, but that's ok. A good mate said "why not just go a mini block v8 and do a twin setup on it. Be cheaper and easier." Of course he's right, but it wouldn't be a 20B - and I want my holy grail =) Besides, v8's are so slow!! hehehehehe
And yes, I am very much aware of the price difference of LPG to Premium... I am about to buy a station wagon (family car) and get a multipoint LPG conversion done to it.
Have a good one!
Pics coming soon. I'm in fatherhood mode atm... Work, take care of bub, pay bills - and the cycle repeats!
But every few days I get some toy time =))
Seriously, I was thinking e85 was so great that it negated the need to go LPG. Lately I have been reconsidering the LPG scenario; but I'm not "there" yet. I'm going to get the emissions test done on metho - as I think it's the only way to pass it on liquid fuel. What you touched on re efficient idling is so true and also the tip of the 20B iceberg. They are a *very* dirty engine. I enabled the 14.4 afr closed loop in the Wolf V500 up to 40% load and watched how it ran... Um... Well it wouldn't idle for a start! The 20B with no porting is dirty. The 20B with mild porting is *very* dirty, and the logic continues... It's simply this: It WANTS to run rich... So yeah... It's a challange.
After it passes engineering (only emissions is holding it back now), I will be sitting down with a dyno and tuner and doing the water injection. I'll keep running 98ron, but I will be able to do a leaner tune with the water injection...
This project has been a challange and a half, but that's ok. A good mate said "why not just go a mini block v8 and do a twin setup on it. Be cheaper and easier." Of course he's right, but it wouldn't be a 20B - and I want my holy grail =) Besides, v8's are so slow!! hehehehehe
And yes, I am very much aware of the price difference of LPG to Premium... I am about to buy a station wagon (family car) and get a multipoint LPG conversion done to it.
Have a good one!
Pics coming soon. I'm in fatherhood mode atm... Work, take care of bub, pay bills - and the cycle repeats!

Last edited by TDIT; 08-08-12 at 07:33 AM. Reason: I'm out of JB - can't think sober!
#79
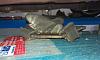
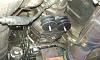
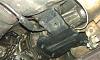
Dear guys and gals,
As promised, here is my solution to the weak stock gearbox mounts. Pics include, what was in place, and obviously what I did to make it a hell of a lot stronger. This resolved a lot of the "slackness" I had present when pulling away and shifting gears.
The new ones are: New to suite a mid 80's Land Rover.
What I needed to do:
1) Make up a steel bracket which attaches to the stock mounting bracket.
2) Tap out the two threads in the bottom of the gearbox to 8mm thread.
Both jobs, easy with a little skill and patience. Or get your local engineer to make up a like bracket out of thick high grade steel.
End result: Strong as houses. Unlikely to ever need be done again.
I ended up changing the engine mounts afterwards as, due to the broken gearbox mount, an engine mount also let go. Now GB and engine mounts have been changed, and my pull away rock has been greatly reduced. It still exists however, so I'm taking it to a rotary shop this week to get them to cast an eye over it and tell me what I have missed - or what they feel is the cause. The shop BTW, is a new one I have not been to previously, but they have a great reputation for building fast drag cars - so I'm guessing they can a) tune really well, and b) eliminate transition slop.
Will post the reults! Enjoy the pics, comments welcome.
#80
Quick update folks - yesterday finally changed the front springs. Back to factory height springs(+1 pound on spring rate from standard.) Car now sits almost at standard height - still a touch lower than normal, but that's ideal. Tells me I've almost compensated for the extra weight, without going too high or hard on the front end. Handling around corners is not noticably different, and body roll remans all but non-existant. That may change on the track, but this isn't a track car.
Best part is the intercooler doesn't bottom out when going up driveways anymore. I'd already had to pull it off and straighten the bracket mounts once already - be damned if I was going to do that again.
Next on the list is the emmisions test. Will be a few weeks though, I'm back in dad mode =)
Cheers!
Best part is the intercooler doesn't bottom out when going up driveways anymore. I'd already had to pull it off and straighten the bracket mounts once already - be damned if I was going to do that again.
Next on the list is the emmisions test. Will be a few weeks though, I'm back in dad mode =)
Cheers!
#81
Hi all,
I took the car to the rotary shop and was extremely impressed with their knowledge. 5 minutes in the car and they identified my problems.
a) I had a jerking feeling when I gently accellerated from low revs. I thought it was a sticking throttle cable - as that's exactly what it felt like. But I couldn't reproduce it with the engine off. Turned out the secondary injectors were comming in too aggressively at low load and rpm. An easy re-tune solution using the afr as a guide at low load and rpm solved the problem.
b) Clutch slop - noticed this when I would pull away or change from 1st to 2nd. I know twin plates clatter, but this wasn't just the plates moving against the centre plate - it was far more aggressive. Result is: It's most likely a combination of the thrust bearing and dif wear - dif bushes are also old. So the combined slop is being felt at the front of the gearbox. Doesn't surprise me at all, and I think they are right on the money. I'm changing the box in the car... I think I have mentioned I have a rebuilt spare. It's just a case of finding the time to do it. Won't be this month I can tell you!
Got to say to anyone considering a 20B conversion. It's awesome to drive - even limited to 5psi and 4500 rpm. As an experience it's hard to describe... Ever driven a car with a caravan or heavily loaded trailer attached - then you remove the dead weight and you feel like you're driving an F1 car? That's the difference I have found going from a 13BT to 20BT. It's a big difference - honestly, it's magic!
I took the car to the rotary shop and was extremely impressed with their knowledge. 5 minutes in the car and they identified my problems.
a) I had a jerking feeling when I gently accellerated from low revs. I thought it was a sticking throttle cable - as that's exactly what it felt like. But I couldn't reproduce it with the engine off. Turned out the secondary injectors were comming in too aggressively at low load and rpm. An easy re-tune solution using the afr as a guide at low load and rpm solved the problem.
b) Clutch slop - noticed this when I would pull away or change from 1st to 2nd. I know twin plates clatter, but this wasn't just the plates moving against the centre plate - it was far more aggressive. Result is: It's most likely a combination of the thrust bearing and dif wear - dif bushes are also old. So the combined slop is being felt at the front of the gearbox. Doesn't surprise me at all, and I think they are right on the money. I'm changing the box in the car... I think I have mentioned I have a rebuilt spare. It's just a case of finding the time to do it. Won't be this month I can tell you!
Got to say to anyone considering a 20B conversion. It's awesome to drive - even limited to 5psi and 4500 rpm. As an experience it's hard to describe... Ever driven a car with a caravan or heavily loaded trailer attached - then you remove the dead weight and you feel like you're driving an F1 car? That's the difference I have found going from a 13BT to 20BT. It's a big difference - honestly, it's magic!
Last edited by TDIT; 09-11-12 at 05:17 AM. Reason: I'm lost in time remember...
#82
Very good info!!
Small remark on the hoodscoop: I think it is working worse than you would hope, due to the fact that the area where it exits in front of the windshield is a 'high pressure' zone, it becomes clear if you look for some picture of pressure distribution on a car surface.
for the HC emissions, it should be no problem imo if the cats are lighted off to cure a few thousand PPM of HC, once burning and making sure there is still a lean lambda after the car, the efficiency should easily be in the 95-99% range
Offcourse you need some decent aux air injection, as the engine probaly won't burn well with lambda around or leaner than one at such low load, ideally you have a closed loop control for engien out lambda, lets say afrs of 13-13.5 so it bruns stable, then control the aux air injection to achieve slightly over lambda one after the cats, this should burn the HC's easily. if you do not have enough aux air injection there is no oxygen to burn the HC's in the cat
Small remark on the hoodscoop: I think it is working worse than you would hope, due to the fact that the area where it exits in front of the windshield is a 'high pressure' zone, it becomes clear if you look for some picture of pressure distribution on a car surface.
for the HC emissions, it should be no problem imo if the cats are lighted off to cure a few thousand PPM of HC, once burning and making sure there is still a lean lambda after the car, the efficiency should easily be in the 95-99% range
Offcourse you need some decent aux air injection, as the engine probaly won't burn well with lambda around or leaner than one at such low load, ideally you have a closed loop control for engien out lambda, lets say afrs of 13-13.5 so it bruns stable, then control the aux air injection to achieve slightly over lambda one after the cats, this should burn the HC's easily. if you do not have enough aux air injection there is no oxygen to burn the HC's in the cat
#83
Hey buddy, thanks for the comments!
I note your comments re the hood scoop. But I think the fact that it's there has changed things a bit for the aerodynamics of the area. When I'm at or above the 90k mark, the bonnet starts to lift a little. At 120 it's sitting "up" at its maximum slop travel (about a centimetre at the front), and stays there until I slow down or sit in messy air - such as behind a truck.
When it was very cold during winter (before I had the heater working), the windscreen would fog up often when even slightly rained. The "only" section that didn't was the area behind the scoop. As soon as I got on the open road and sat on 80ks for a bit, the clear patch would extend all the way to the top of the windshield like a wide stripe - leaving the left and right sides still fogged. Eventually everything would clear, but the cycle was repeated often.
The fact that the scoop is there means that directly behind it will become a turbulent low pressure area which will increase the faster I go. This is because there is a high pressure area on the bonnet itself, a higher pressure area as the air is forced up and over the scoop, then a massive drop with the turbulance of the now dirty air as the air passes over the opening of the scoop, before it then hits the windscreen and turns back into a high pressure area. It's the turblance which creates the low pressure area, which literally sucks the air from in the engine bay and out of the scoop - to then mix with the cooler air passing up the windscreen.
I had a low pressure high volume pump installed to feed air to the cats. This was after I cut down three Lukey high density cats and made them into one large cat. In every test - with differing amounts of air flow (from quite high to extremely low) - and the use of a 5 gas analyser, the addition of the fresh air had a negative effect on the cats performance. We concluded that the problem was that the cold air was putting the cats out, rather than allowing them to lite up further.
What did you get your HC ppm down to? Here even 900 ppm is way too high. The objective for me to get the car legal here is to reduce the Hydrocarbons to approximately 100-150 PPM - but that's not the way it is measured for legalities here. To pass here it's measured as an amount of grams / kilometre. I honestly believe that passing isn't possible with a mild ported 20BT, if it's running on un-ethanol blended pump fuel. That's why I'm going to do the test itself on pure ethanol - with the boost dumped and the secondaries off.
I'm re-tuning low load using the afr as a guide currently. So far I can cruise below 30% load at 13.7 to 14.2 afr. I have an ems problem atm that I'm working through - and need to fix before I can safely enable the closed loop again. Once done I will again be able to resume my closed loop testing. I'm very hopeful I can get the closed loop working at low load. I feel it will solve a few minor problems and one big one.
Previously the car would not idle on closed loop and even under low load ran horribly - so it didn't stay turned on for long. I think part of that was the large secondaries being still enabled, and aggressively so. But I couldn;t tuen them off at the time or the primary duty cycle was way too high.
Right now - i.e.: yesterday and today - I installed a simple air flow restricting load limiter (adjusting it so its impossible to load the engine past about 35%.) I've dumped the boost (it will hold about a pound then open the gate), and I've disabled the secondary injectors and have the car idling well at an afr of 12. That's as far as I've gone today - ran out of time. The car is off the road during this stage. I can easily remove the restrictor and load the running map if I need to use it in a hurry.
I'll of course post the results.
I'm hopeful (extremely hopeful) that this time I will have done enough to get passed!!
Cheers!
I note your comments re the hood scoop. But I think the fact that it's there has changed things a bit for the aerodynamics of the area. When I'm at or above the 90k mark, the bonnet starts to lift a little. At 120 it's sitting "up" at its maximum slop travel (about a centimetre at the front), and stays there until I slow down or sit in messy air - such as behind a truck.
When it was very cold during winter (before I had the heater working), the windscreen would fog up often when even slightly rained. The "only" section that didn't was the area behind the scoop. As soon as I got on the open road and sat on 80ks for a bit, the clear patch would extend all the way to the top of the windshield like a wide stripe - leaving the left and right sides still fogged. Eventually everything would clear, but the cycle was repeated often.
The fact that the scoop is there means that directly behind it will become a turbulent low pressure area which will increase the faster I go. This is because there is a high pressure area on the bonnet itself, a higher pressure area as the air is forced up and over the scoop, then a massive drop with the turbulance of the now dirty air as the air passes over the opening of the scoop, before it then hits the windscreen and turns back into a high pressure area. It's the turblance which creates the low pressure area, which literally sucks the air from in the engine bay and out of the scoop - to then mix with the cooler air passing up the windscreen.
I had a low pressure high volume pump installed to feed air to the cats. This was after I cut down three Lukey high density cats and made them into one large cat. In every test - with differing amounts of air flow (from quite high to extremely low) - and the use of a 5 gas analyser, the addition of the fresh air had a negative effect on the cats performance. We concluded that the problem was that the cold air was putting the cats out, rather than allowing them to lite up further.
What did you get your HC ppm down to? Here even 900 ppm is way too high. The objective for me to get the car legal here is to reduce the Hydrocarbons to approximately 100-150 PPM - but that's not the way it is measured for legalities here. To pass here it's measured as an amount of grams / kilometre. I honestly believe that passing isn't possible with a mild ported 20BT, if it's running on un-ethanol blended pump fuel. That's why I'm going to do the test itself on pure ethanol - with the boost dumped and the secondaries off.
I'm re-tuning low load using the afr as a guide currently. So far I can cruise below 30% load at 13.7 to 14.2 afr. I have an ems problem atm that I'm working through - and need to fix before I can safely enable the closed loop again. Once done I will again be able to resume my closed loop testing. I'm very hopeful I can get the closed loop working at low load. I feel it will solve a few minor problems and one big one.
Previously the car would not idle on closed loop and even under low load ran horribly - so it didn't stay turned on for long. I think part of that was the large secondaries being still enabled, and aggressively so. But I couldn;t tuen them off at the time or the primary duty cycle was way too high.
Right now - i.e.: yesterday and today - I installed a simple air flow restricting load limiter (adjusting it so its impossible to load the engine past about 35%.) I've dumped the boost (it will hold about a pound then open the gate), and I've disabled the secondary injectors and have the car idling well at an afr of 12. That's as far as I've gone today - ran out of time. The car is off the road during this stage. I can easily remove the restrictor and load the running map if I need to use it in a hurry.
I'll of course post the results.
I'm hopeful (extremely hopeful) that this time I will have done enough to get passed!!
Cheers!
Last edited by TDIT; 09-18-12 at 06:38 AM. Reason: typo
#84
Hi, the reasons why the hood comes up is the overal differential pressure acting on the area of the hood (=force) is in the favor of pusing it up: which means: pressure * area under the hood > pressure * area aobve the hood caused by
a: lower pressure at the front/middle above hood, due to the faster travelling air there
b: higher pressure under the hood due to the fact that scoop opening is in a high pressure zone, combined with the pressure created from the flow trough the radiator/indercooler
About the HC's, have you measured lambda after the cat and temperature after (or better in) the cat? if its below lambda one, there is not enough oxygen to burn the HC, if its way too lean, you'll blow the cat out.. good rule of thumb is to increase aux air injection until you see the in-cat temperature go down, and from there back a bit off again till you reach the highest deltaT over the cat. also there are not too much cats that will live long with the temperatures of a rotary, so if the cats/metal loading isn't designed for the temperatures, the efficiency will be gone in a matter of hours
a: lower pressure at the front/middle above hood, due to the faster travelling air there
b: higher pressure under the hood due to the fact that scoop opening is in a high pressure zone, combined with the pressure created from the flow trough the radiator/indercooler
About the HC's, have you measured lambda after the cat and temperature after (or better in) the cat? if its below lambda one, there is not enough oxygen to burn the HC, if its way too lean, you'll blow the cat out.. good rule of thumb is to increase aux air injection until you see the in-cat temperature go down, and from there back a bit off again till you reach the highest deltaT over the cat. also there are not too much cats that will live long with the temperatures of a rotary, so if the cats/metal loading isn't designed for the temperatures, the efficiency will be gone in a matter of hours
#85
Hiya =)
I'm not sure I agree with the pressure zoning of the bonnet & scoop, but however it's flowing, it's working so I'm very happy in that regard. =)
The sensor I have has to go before the cat. All the testing done on the dyno was well after the cat - about a meter in from the end. Your logic re the cat temp and air flow is very useful information - thank you =) If all my other efforts fail I will re-visit the air pump and find a way of measuring the temp within. Things like your rule of thumb are extremely valuable to everyone here =)
If you read back through the thread (have a beer ready
you'll see that the existing section containing the cats is only in place to slow down the gases and pass emissions. Originally I had two 3.5 (or were they 4") MetalCats in series for emmisions control. Simply put they were utterly useless. That was why I went with a modiefied high density metal cat (the element, not the brand) instead of ceramic. It's not needed to last long (and remember the car is severely limited atm [2.5 exhaust leading to the cat, 4.5 rev limit, 5 pound of boost]), and objectively the steel cats work better than the ceramic - but don't last as long. Once the car passes emissions the sections will be swapped back and I'll run the metal cats again, so I have far less exhaust back pressure. That will be when I start running more boost up too 8k rpm and not care about how much hc goes out the back. Sorry environment...
Cheers!
I'm not sure I agree with the pressure zoning of the bonnet & scoop, but however it's flowing, it's working so I'm very happy in that regard. =)
The sensor I have has to go before the cat. All the testing done on the dyno was well after the cat - about a meter in from the end. Your logic re the cat temp and air flow is very useful information - thank you =) If all my other efforts fail I will re-visit the air pump and find a way of measuring the temp within. Things like your rule of thumb are extremely valuable to everyone here =)
If you read back through the thread (have a beer ready

Cheers!
#86
Hi all!!
Quick update - 0.7psi of boost from an extra 250rpm/ Stoich state (closed loop)/ Over run/ Idle adjustment/ front bar/ bonnet.
I've upped the rev limit to 5000rpm now that the car has done over 2000k's. I've only gone to 5000 as that was as high as the original dyno tune went to. Prior to that I was running 4750 and was maxing out at 7.5 psi under full load. With the extra 250rpm I'm maxing out at 8.2psi. That's a nice improvement for a few extra revs!
After a lot of testing time to find the right balance, I have a closed loop enabled on the 20BT. I'm running CL from 1800rpm to 5000rpm with it only enabled at outside air pressure LESS 15%. Translation: Closed loop is only active under vacuum. By the time it approaches equal pressure (zero boost and vacuum), the CL is already off. Can't run it at idle as I've managed to get the car to idle with it, but it's too lean for my porting, so 1800 it is. CL is only active in the above condition and when engine temp is 82c or higher.
Overrun fuel cut is also enabled above 82c and from 5000rpm down to 1750rpm (it's important to make the ORFC finish after the CL. I have programed a cuple of recovery injector pulses when ORFC finishes (to avoid the stall that can occur.) Getting this right was actually harder than the CL config - as the computer does most of the work with the CL, whch the OR setup and recovery setup is up to us.
Idle adjustment shouldn't be worth a mention surely? Well, I'm mentioning it because one rotory workshop told me there wasn't one there - and my only adjustment options were the air by-pass screw on top of the manifold, or to install an idle step solinoid and have the computer manage it. Dumb!!
Okay folks, listen up. If you're looking for the easy way to adjust your idle on a 20B, and possibly 13B's with like intakes, use the screw on the top of the manifold. Screw it in to lower the idle - this closes the path allowing air to by-pass the butterfly valve. If you need a higher idle, undo the screw as much as you need to (noting that there will come a point it will come out), remembering that once the idle comes up to the highest point there is no need to open it further. If you need more adjustment - say your idle is too low, then do this:
1) warm up the car and then screw out your air bypass screw as much as possible without letting it come loose or out.
2) come to the front (FRONT!!) of the manifold (NOT THE REAR WHERE THE THROTTLE CABLE IS) and look for a small flat headded screw in an impossible position near the butterful shaft. You will need to customise a tool to turn it, or have a tiny flat blade to turn it form the side.
3) Turn it clockwise until you have an idle that is too high - then stop.
4) now screw back in the air bypass screw until you reach the desired idle.
5) give the gas a few taps to balance out the valve, then adjust screw as needed.
The front bar of the S5 is becomes an air restriction issue *if* you don’t move the engine back when doing a 20B conversion and accordingly use a vertical radiator. If you’re read the full thread (thank you) then you’ll know I choose not to move it back, but instead made room in the front. The question that was raised at the time (even with the large cross flow radiator) was will their be enough clean air getting to the radiator for efficient head exchange. The answer, quite simply, is no. It’s not an issue with placement, nor core size, fan size or water pump type. It’s simply a case of air flow. The stock radiator was at a slant, to get max air flow through the available front bar/grill. As soon as you sit one upright, you are straight away limiting the top section – as there is no substantial airflow to it. As the weather became warmer, my running temp crept up from 90-91 to 93-94. They were the minimum running temps. Sitting on the highway at 65 miles would take it to 97-98. Clearly too high for a minimum temp. My solution is to open up the front bar and duct air into the radiator. I have found a custom body worker to do the job for me. His reputation is solid and he’s local (f’ing yay!!) Will post pics of the results and temp differences.
Bonnet:
This ties into the above point, but when the front is opened up, I will need new ways for the air to get out, as there is no point opening up the front and then stopping. Air needs to flow. Not come in and get bogged down looking for a place to get out. All that does is create turbulence and slow down the incoming air. As a result I will be adding bonnet vents to allow both air and heat out of the bay. Pics and results when done.
Have to say; now that I have a cruise afr of around 14.7:1, fuel consumption has reduced about a ¼. So instead of getting around 220k’s around the suburbs, it’s now getting to 280 on 98ron. When I can get the temp down I’ll have a little more efficiency also. Oh, and the most important part: When I plant the right foot the scenery blurs and I’m pushed back into the seat. Gear change, same result, and again… Opps – how fast? Brake now =)
That’s it for now!
Cheers!
Quick update - 0.7psi of boost from an extra 250rpm/ Stoich state (closed loop)/ Over run/ Idle adjustment/ front bar/ bonnet.
I've upped the rev limit to 5000rpm now that the car has done over 2000k's. I've only gone to 5000 as that was as high as the original dyno tune went to. Prior to that I was running 4750 and was maxing out at 7.5 psi under full load. With the extra 250rpm I'm maxing out at 8.2psi. That's a nice improvement for a few extra revs!
After a lot of testing time to find the right balance, I have a closed loop enabled on the 20BT. I'm running CL from 1800rpm to 5000rpm with it only enabled at outside air pressure LESS 15%. Translation: Closed loop is only active under vacuum. By the time it approaches equal pressure (zero boost and vacuum), the CL is already off. Can't run it at idle as I've managed to get the car to idle with it, but it's too lean for my porting, so 1800 it is. CL is only active in the above condition and when engine temp is 82c or higher.
Overrun fuel cut is also enabled above 82c and from 5000rpm down to 1750rpm (it's important to make the ORFC finish after the CL. I have programed a cuple of recovery injector pulses when ORFC finishes (to avoid the stall that can occur.) Getting this right was actually harder than the CL config - as the computer does most of the work with the CL, whch the OR setup and recovery setup is up to us.
Idle adjustment shouldn't be worth a mention surely? Well, I'm mentioning it because one rotory workshop told me there wasn't one there - and my only adjustment options were the air by-pass screw on top of the manifold, or to install an idle step solinoid and have the computer manage it. Dumb!!
Okay folks, listen up. If you're looking for the easy way to adjust your idle on a 20B, and possibly 13B's with like intakes, use the screw on the top of the manifold. Screw it in to lower the idle - this closes the path allowing air to by-pass the butterfly valve. If you need a higher idle, undo the screw as much as you need to (noting that there will come a point it will come out), remembering that once the idle comes up to the highest point there is no need to open it further. If you need more adjustment - say your idle is too low, then do this:
1) warm up the car and then screw out your air bypass screw as much as possible without letting it come loose or out.
2) come to the front (FRONT!!) of the manifold (NOT THE REAR WHERE THE THROTTLE CABLE IS) and look for a small flat headded screw in an impossible position near the butterful shaft. You will need to customise a tool to turn it, or have a tiny flat blade to turn it form the side.
3) Turn it clockwise until you have an idle that is too high - then stop.
4) now screw back in the air bypass screw until you reach the desired idle.
5) give the gas a few taps to balance out the valve, then adjust screw as needed.
The front bar of the S5 is becomes an air restriction issue *if* you don’t move the engine back when doing a 20B conversion and accordingly use a vertical radiator. If you’re read the full thread (thank you) then you’ll know I choose not to move it back, but instead made room in the front. The question that was raised at the time (even with the large cross flow radiator) was will their be enough clean air getting to the radiator for efficient head exchange. The answer, quite simply, is no. It’s not an issue with placement, nor core size, fan size or water pump type. It’s simply a case of air flow. The stock radiator was at a slant, to get max air flow through the available front bar/grill. As soon as you sit one upright, you are straight away limiting the top section – as there is no substantial airflow to it. As the weather became warmer, my running temp crept up from 90-91 to 93-94. They were the minimum running temps. Sitting on the highway at 65 miles would take it to 97-98. Clearly too high for a minimum temp. My solution is to open up the front bar and duct air into the radiator. I have found a custom body worker to do the job for me. His reputation is solid and he’s local (f’ing yay!!) Will post pics of the results and temp differences.
Bonnet:
This ties into the above point, but when the front is opened up, I will need new ways for the air to get out, as there is no point opening up the front and then stopping. Air needs to flow. Not come in and get bogged down looking for a place to get out. All that does is create turbulence and slow down the incoming air. As a result I will be adding bonnet vents to allow both air and heat out of the bay. Pics and results when done.
Have to say; now that I have a cruise afr of around 14.7:1, fuel consumption has reduced about a ¼. So instead of getting around 220k’s around the suburbs, it’s now getting to 280 on 98ron. When I can get the temp down I’ll have a little more efficiency also. Oh, and the most important part: When I plant the right foot the scenery blurs and I’m pushed back into the seat. Gear change, same result, and again… Opps – how fast? Brake now =)
That’s it for now!
Cheers!
#88
Wow. An interesting read for sure. I'm seriously getting sick of road laws & vehicle regs in Australia, it's just pathetic. If speed enforcement in NSW starts becoming akin to Vic, I'll definitely consider moving to a more civilised country.
Have you got the car registered, just not compliant?
Have you got the car registered, just not compliant?
#89
Thanks mate
Yeah, it's fairly insane... Currently I'm registered but not engineered. I'm trying to get that resolved, but atm I'm in the middle of a lengthy legal matter so I have no free time.
On the up side, whenever I need a release, I take the beasty out and practice drifting around large roundabouts. I'm not that great at it, but I am improving
I will post the pics re the open front bar tonight. It made "a" difference, but not enough.
I would like to reverse time for a moment and thank everyone that said that overheating issues would be a major factor. I thought (wrongly) that I wouldn't face these issues. I was wrong - even with my huge radiator and fan. More on this next post!
Cheers everyone!

Yeah, it's fairly insane... Currently I'm registered but not engineered. I'm trying to get that resolved, but atm I'm in the middle of a lengthy legal matter so I have no free time.

On the up side, whenever I need a release, I take the beasty out and practice drifting around large roundabouts. I'm not that great at it, but I am improving

I will post the pics re the open front bar tonight. It made "a" difference, but not enough.
I would like to reverse time for a moment and thank everyone that said that overheating issues would be a major factor. I thought (wrongly) that I wouldn't face these issues. I was wrong - even with my huge radiator and fan. More on this next post!
Cheers everyone!
#90
Hi all!
Sorry, I know I promised pics - they're coming I swear!
I've been doing some reading in what free time I have, but I can't find what I'm looking for. So a super quick question to anyone who knows or can suggest a thread to read:
The transitional lean spot that occurs just as the secondary butterfly opens was annoying me greatly. I couldn't tune around it, so went to mechanical causes and found a thread that talked about it (here) and made reference to extending the linkage arm between the primary and secondary actuators as a solution. Before I go down that road I adjusted the top screw which controls the stop point of the secondary butterfly. I've opened it slightly, meaning the car now idles with air from the primary and secondary butterflies. Naturally that sped up the idle, which I corrected with a simple adjustment of the primary butterfly.
The result I was hoping for was to balance out the air pressure in the manifold, so when the secondary butterfly opened under light load, there was less pressure difference to "upset" the flow and cause the lean point. That result was met, and the lean spot is all but gone, so yay to my logic being of merit in that case. However now I have created an unstable (turbulent) air flow condition on idle, meaning my idle is lumpy and unstable (varies with rich pops - which tuning or timing tweaks can't correct.) Simply because the variance is the air speed via pressure, not the fuel delivery.
It's not the end of the world, the idle doesn't stall or hunt, and has an afr of around 12 to 12.5:1. The car does drive great under low load with an afr of 14.7 to 15:1. But I was wondering if anyone else had a take on this? Another solution maybe?
Just an fyi - the wax valve is still connected to the manifold, but doesn’t have water flowing through it. And I'm not running an idle control valve. <-- Both decisions made by the building rotary shop. I am thinking an idle control valve would resolve the issue. I have the one they took off the engine (somewhere!)
I appreciate comments both in favour and against what I've done. All good. Just be nice
Cheers all!
Sorry, I know I promised pics - they're coming I swear!
I've been doing some reading in what free time I have, but I can't find what I'm looking for. So a super quick question to anyone who knows or can suggest a thread to read:
The transitional lean spot that occurs just as the secondary butterfly opens was annoying me greatly. I couldn't tune around it, so went to mechanical causes and found a thread that talked about it (here) and made reference to extending the linkage arm between the primary and secondary actuators as a solution. Before I go down that road I adjusted the top screw which controls the stop point of the secondary butterfly. I've opened it slightly, meaning the car now idles with air from the primary and secondary butterflies. Naturally that sped up the idle, which I corrected with a simple adjustment of the primary butterfly.
The result I was hoping for was to balance out the air pressure in the manifold, so when the secondary butterfly opened under light load, there was less pressure difference to "upset" the flow and cause the lean point. That result was met, and the lean spot is all but gone, so yay to my logic being of merit in that case. However now I have created an unstable (turbulent) air flow condition on idle, meaning my idle is lumpy and unstable (varies with rich pops - which tuning or timing tweaks can't correct.) Simply because the variance is the air speed via pressure, not the fuel delivery.
It's not the end of the world, the idle doesn't stall or hunt, and has an afr of around 12 to 12.5:1. The car does drive great under low load with an afr of 14.7 to 15:1. But I was wondering if anyone else had a take on this? Another solution maybe?
Just an fyi - the wax valve is still connected to the manifold, but doesn’t have water flowing through it. And I'm not running an idle control valve. <-- Both decisions made by the building rotary shop. I am thinking an idle control valve would resolve the issue. I have the one they took off the engine (somewhere!)
I appreciate comments both in favour and against what I've done. All good. Just be nice

Cheers all!
#92
Hi mate,
Yeah, have turbo =) So everything "happens" after that
I've got it adjusted well enough, but I had a smooth idle before I adjusted the secondary butterfly - which corrected 80% of the transitional lag - so I know I'm not chasing something impossible.
Thanks heaps for your reply and thoughts
Cheers!
Yeah, have turbo =) So everything "happens" after that

I've got it adjusted well enough, but I had a smooth idle before I adjusted the secondary butterfly - which corrected 80% of the transitional lag - so I know I'm not chasing something impossible.
Thanks heaps for your reply and thoughts

Cheers!
#93
Hi all!
Sorry, I know I promised pics - they're coming I swear!
I've been doing some reading in what free time I have, but I can't find what I'm looking for. So a super quick question to anyone who knows or can suggest a thread to read:
The transitional lean spot that occurs just as the secondary butterfly opens was annoying me greatly. I couldn't tune around it, so went to mechanical causes and found a thread that talked about it (here) and made reference to extending the linkage arm between the primary and secondary actuators as a solution. Before I go down that road I adjusted the top screw which controls the stop point of the secondary butterfly. I've opened it slightly, meaning the car now idles with air from the primary and secondary butterflies. Naturally that sped up the idle, which I corrected with a simple adjustment of the primary butterfly.
The result I was hoping for was to balance out the air pressure in the manifold, so when the secondary butterfly opened under light load, there was less pressure difference to "upset" the flow and cause the lean point. That result was met, and the lean spot is all but gone, so yay to my logic being of merit in that case. However now I have created an unstable (turbulent) air flow condition on idle, meaning my idle is lumpy and unstable (varies with rich pops - which tuning or timing tweaks can't correct.) Simply because the variance is the air speed via pressure, not the fuel delivery.
It's not the end of the world, the idle doesn't stall or hunt, and has an afr of around 12 to 12.5:1. The car does drive great under low load with an afr of 14.7 to 15:1. But I was wondering if anyone else had a take on this? Another solution maybe?
Just an fyi - the wax valve is still connected to the manifold, but doesn’t have water flowing through it. And I'm not running an idle control valve. <-- Both decisions made by the building rotary shop. I am thinking an idle control valve would resolve the issue. I have the one they took off the engine (somewhere!)
I appreciate comments both in favour and against what I've done. All good. Just be nice
Cheers all!
Sorry, I know I promised pics - they're coming I swear!
I've been doing some reading in what free time I have, but I can't find what I'm looking for. So a super quick question to anyone who knows or can suggest a thread to read:
The transitional lean spot that occurs just as the secondary butterfly opens was annoying me greatly. I couldn't tune around it, so went to mechanical causes and found a thread that talked about it (here) and made reference to extending the linkage arm between the primary and secondary actuators as a solution. Before I go down that road I adjusted the top screw which controls the stop point of the secondary butterfly. I've opened it slightly, meaning the car now idles with air from the primary and secondary butterflies. Naturally that sped up the idle, which I corrected with a simple adjustment of the primary butterfly.
The result I was hoping for was to balance out the air pressure in the manifold, so when the secondary butterfly opened under light load, there was less pressure difference to "upset" the flow and cause the lean point. That result was met, and the lean spot is all but gone, so yay to my logic being of merit in that case. However now I have created an unstable (turbulent) air flow condition on idle, meaning my idle is lumpy and unstable (varies with rich pops - which tuning or timing tweaks can't correct.) Simply because the variance is the air speed via pressure, not the fuel delivery.
It's not the end of the world, the idle doesn't stall or hunt, and has an afr of around 12 to 12.5:1. The car does drive great under low load with an afr of 14.7 to 15:1. But I was wondering if anyone else had a take on this? Another solution maybe?
Just an fyi - the wax valve is still connected to the manifold, but doesn’t have water flowing through it. And I'm not running an idle control valve. <-- Both decisions made by the building rotary shop. I am thinking an idle control valve would resolve the issue. I have the one they took off the engine (somewhere!)
I appreciate comments both in favour and against what I've done. All good. Just be nice

Cheers all!
Just letting anyone that is looking for a resolution to this problem, here's mine:
In the Wolf V500 (and V550 and probably other ems's) you can simulate a throttle pump's operation. Meaning you can squirt a little more fuel into the chamber just as the throttle is opened under different load states. So to cater for the lean spot on progression from primary to secondary butterflys, I added 30% more fuel at low loads, reducing via gradiant to 10% on medium loads with a high decay rate. There is no adjustment needed on high loads as the secondary butterfly is well and truly open and the problem doesn't exist.
The net result is the lean patch is met with a slightly greater rich spot, so afr is almost exactly maintained in a gradule curve. I've tweaked it under light and medium load on the road and I'm happy with the results. So now I have gone back to my original idle and secondary adjustment (which gave near perfect idle) and has reduced the transitional lean spot to a point it's only just noticable.
Back to tuning for emissions!!

#95
Hi mate,
Thought about exhaust recycling and really don't want to - unless absolutely necessary. I think if I run NA, without secondaries and with e85 (a horrible but mostly ethanol fuel), I should pass.
I'm planning to do water injection (to come on when the secondaries are in use), but not for prior load points (as I'll go through too much too fast and end up with a lean out if I'm not very watchful.) I may be paranoid, but...
I'm going to go down the larger water volume route first, in time for next summer, and hopefully that will be the end of my water temp issues!
Thanks for your thoughts and post =) Appreciate the input
Cheers!
Thought about exhaust recycling and really don't want to - unless absolutely necessary. I think if I run NA, without secondaries and with e85 (a horrible but mostly ethanol fuel), I should pass.
I'm planning to do water injection (to come on when the secondaries are in use), but not for prior load points (as I'll go through too much too fast and end up with a lean out if I'm not very watchful.) I may be paranoid, but...

I'm going to go down the larger water volume route first, in time for next summer, and hopefully that will be the end of my water temp issues!
Thanks for your thoughts and post =) Appreciate the input

Cheers!
#96
Was thinking water injection for cooling the combustion. As I understand it, a large part of the reason for terrible emissions is excessive combustion/exhaust temps. A bit of water should keep that lowish and force out carbon dioxides rather than the other mess.
#97
Hi mate,
I knew what you meant (water injection for cooling), but I'm only going to do it for when on boost so I can run leaner without risk. If I run water injection all the time I'll need a lot of water =) Re emmisions, yes, water injection helps also (I'm hoping I won't need to), but remember the CAT's need heat to convert the bad stuff into the okay stuff. Ideally the CAT should be much closer than about 100cm behind the turbo - but for space issues it's not practical.
Gotta dash - loads to do today
Cheers for your replies and thoughts =)
I knew what you meant (water injection for cooling), but I'm only going to do it for when on boost so I can run leaner without risk. If I run water injection all the time I'll need a lot of water =) Re emmisions, yes, water injection helps also (I'm hoping I won't need to), but remember the CAT's need heat to convert the bad stuff into the okay stuff. Ideally the CAT should be much closer than about 100cm behind the turbo - but for space issues it's not practical.
Gotta dash - loads to do today

Cheers for your replies and thoughts =)
#98
Greetings to all!
I seriously cannot believe it's been 4 years since I updated this thread. To anyone still following it, a) thank you
and b) I'm sorry! I have two kids now and damn the free time has vanished.
But, I'm bringing it all back. The car has been in storage. It failed emissions again and again. I was so sick of it I considered selling it. If the rotary shop that did the farming out work were still in business (they went broke years ago) I would have had at them. But the situation is what it is.
Did the metho fuel come close to passing emissions? Yes, but I was still nearly three times the adr limit for CO and it ran badly on idle no matter what I did. To be honest I was happy to flush that fuel out of the system. Unfortunately I left it in there for a week before I did the flush, and although it wasn't an obvious problem, all my fuel lines perished within a few months afterwards. I replaced them all with lines rated to handle ethanol inside AND out. This meant the lines I had in the tank would survive being submerged in fuel - no matter what I ran.
Before I revisit the emission issue, I'm going to do everything the car needs that I put off in lieu of solving emissions first. That includes fixing the overheating issue with both ducking and a second water reservoir. There is an after boil issue however. Solving that will be via either running an inline electric water pump (which will both aid flow as well) and prevent after boil as I'll set it to run for 5 minutes after the engine is off, OR I'll just run Evans coolant. Both solutions will resolve the after-boil issue, but although Evans will reduce the pressure load on the cooling system, it isn't as efficient as water and coolant when it comes to removing heat. I'll add the ducting and second reservoir then see how it goes. I may even put in place another radiator, if I can find a place to stick one.
I'll update as stuff is done, because it's fun
Does anyone have a good lead on a carbon fiber sunroof replacement for the FC Series 5? mine is unsightly and rusted again. I see there are a few on ebay, but I was wondering if anyone reading this had a suggestion. Yes I'll do some searching through the forum now also
Cheers!
I seriously cannot believe it's been 4 years since I updated this thread. To anyone still following it, a) thank you

But, I'm bringing it all back. The car has been in storage. It failed emissions again and again. I was so sick of it I considered selling it. If the rotary shop that did the farming out work were still in business (they went broke years ago) I would have had at them. But the situation is what it is.
Did the metho fuel come close to passing emissions? Yes, but I was still nearly three times the adr limit for CO and it ran badly on idle no matter what I did. To be honest I was happy to flush that fuel out of the system. Unfortunately I left it in there for a week before I did the flush, and although it wasn't an obvious problem, all my fuel lines perished within a few months afterwards. I replaced them all with lines rated to handle ethanol inside AND out. This meant the lines I had in the tank would survive being submerged in fuel - no matter what I ran.
Before I revisit the emission issue, I'm going to do everything the car needs that I put off in lieu of solving emissions first. That includes fixing the overheating issue with both ducking and a second water reservoir. There is an after boil issue however. Solving that will be via either running an inline electric water pump (which will both aid flow as well) and prevent after boil as I'll set it to run for 5 minutes after the engine is off, OR I'll just run Evans coolant. Both solutions will resolve the after-boil issue, but although Evans will reduce the pressure load on the cooling system, it isn't as efficient as water and coolant when it comes to removing heat. I'll add the ducting and second reservoir then see how it goes. I may even put in place another radiator, if I can find a place to stick one.
I'll update as stuff is done, because it's fun

Does anyone have a good lead on a carbon fiber sunroof replacement for the FC Series 5? mine is unsightly and rusted again. I see there are a few on ebay, but I was wondering if anyone reading this had a suggestion. Yes I'll do some searching through the forum now also

Cheers!