Wiper arm mod
#1
Thread Starter
Stigulus Moderatorai
iTrader: (3)
Joined: Feb 2004
Posts: 2,107
Likes: 29
From: Canada
Wiper arm mod
So I was tired of the stupid pin design on our wiper blades. As it wipes across the glass, the blade assembly has so much play that it drags the blade at an angle and also causes it to skip across the window.
It appears that Mazda only used that pin design on the first gen, as all their cars afterwards used a hook. This hook is the current way nearly every modern car uses, so it must be decent. It also minimizes the back and forth play that was present in the pin design.
I bought some 626 wiper arms from the junkyard that used the hook design. Unfortunately these a both slightly thicker and wider than our arms, but I took up the extra by cutting the stock arms at the bend. I don't think you can really notice.
So I cut the stock arms right at the bend. I also drilled a hole 1/3 the width of the stock arm right at the cut point. By doing this to both pieces, I had more surface area for my welds, especially after grinding. I also beveled the edges to ensure that I would get a solid weld.
From the center of the hook, I measured 4mm and did the same cutting and drilling procedure. The two pieces were then welded, grinded, filed and smoothed before a few coats of filler primer and a semigloss topcoat.
Old arms on bottom with new hooks welded to a spare set of arms:
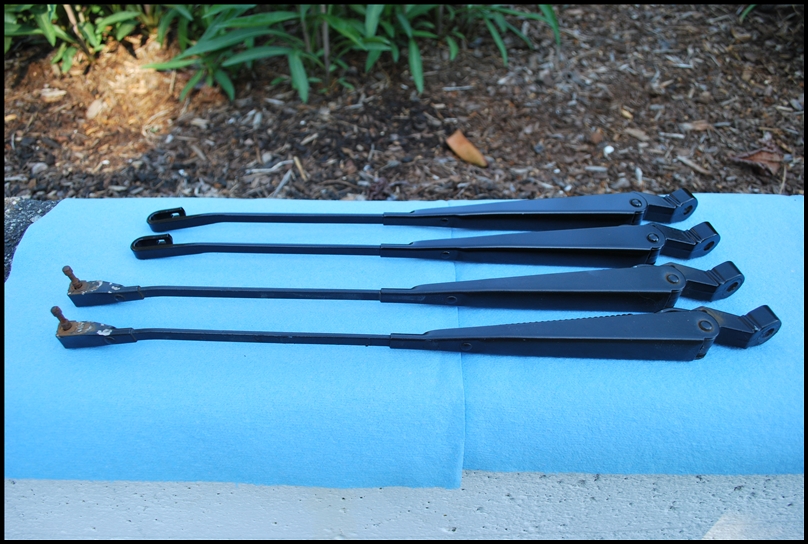
They are shorter, but this is to account for the difference in mounting. The blade sits in the same location on the car.
Hooks:
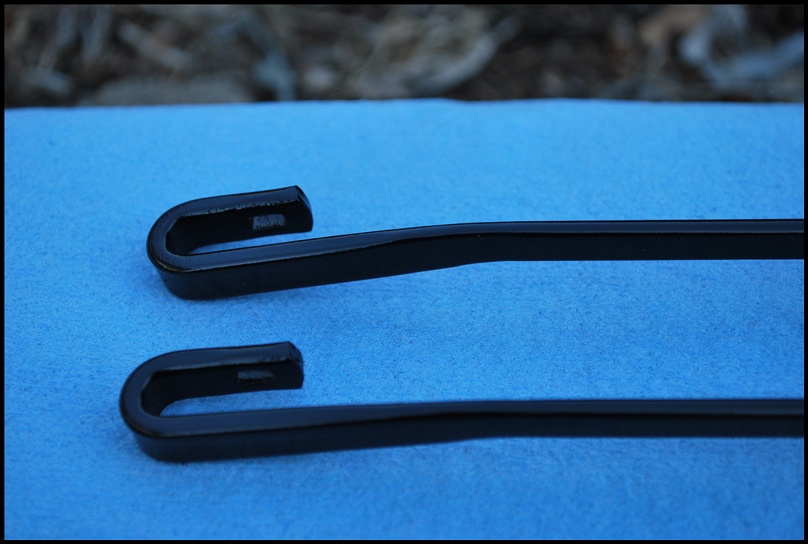
Bloody pins:
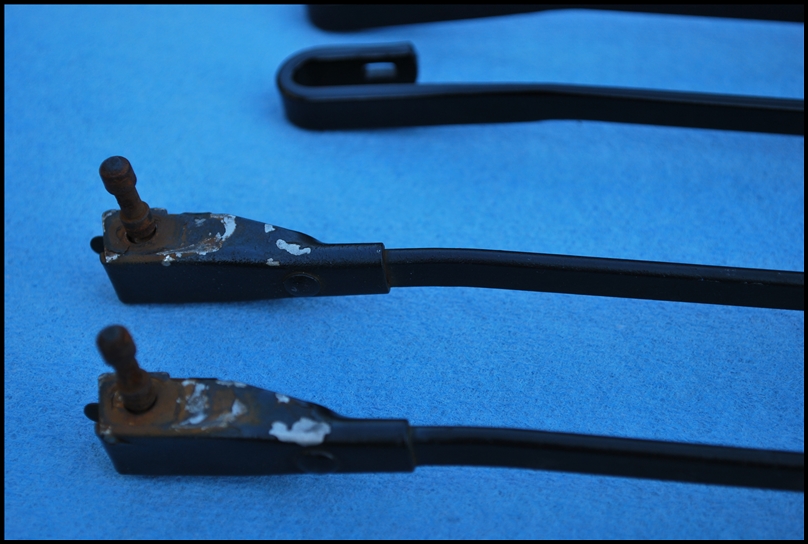
And the final product:
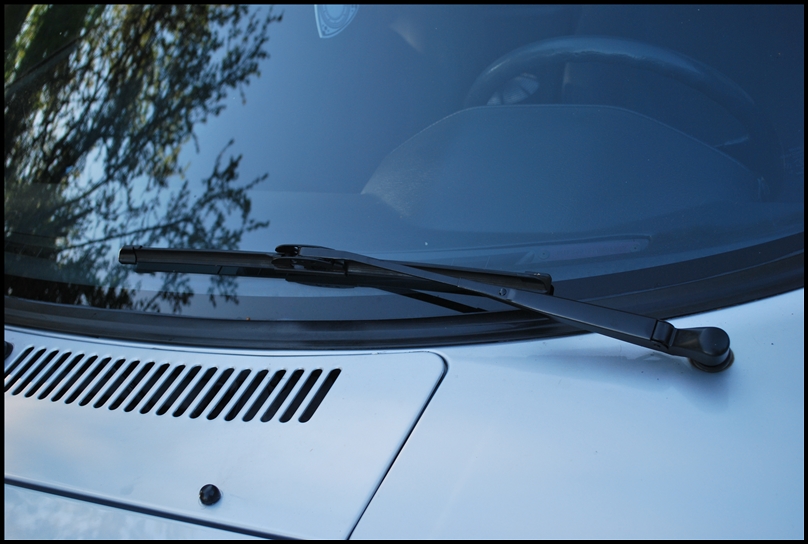

It appears that Mazda only used that pin design on the first gen, as all their cars afterwards used a hook. This hook is the current way nearly every modern car uses, so it must be decent. It also minimizes the back and forth play that was present in the pin design.
I bought some 626 wiper arms from the junkyard that used the hook design. Unfortunately these a both slightly thicker and wider than our arms, but I took up the extra by cutting the stock arms at the bend. I don't think you can really notice.
So I cut the stock arms right at the bend. I also drilled a hole 1/3 the width of the stock arm right at the cut point. By doing this to both pieces, I had more surface area for my welds, especially after grinding. I also beveled the edges to ensure that I would get a solid weld.
From the center of the hook, I measured 4mm and did the same cutting and drilling procedure. The two pieces were then welded, grinded, filed and smoothed before a few coats of filler primer and a semigloss topcoat.
Old arms on bottom with new hooks welded to a spare set of arms:
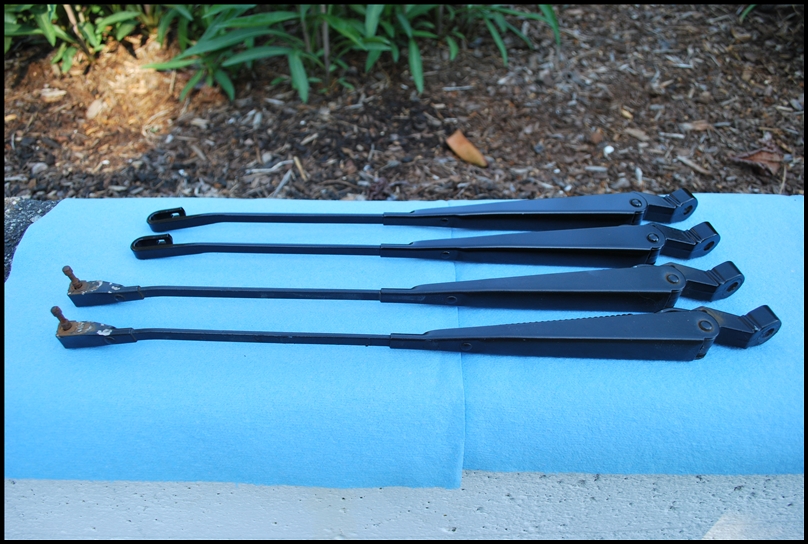
They are shorter, but this is to account for the difference in mounting. The blade sits in the same location on the car.
Hooks:
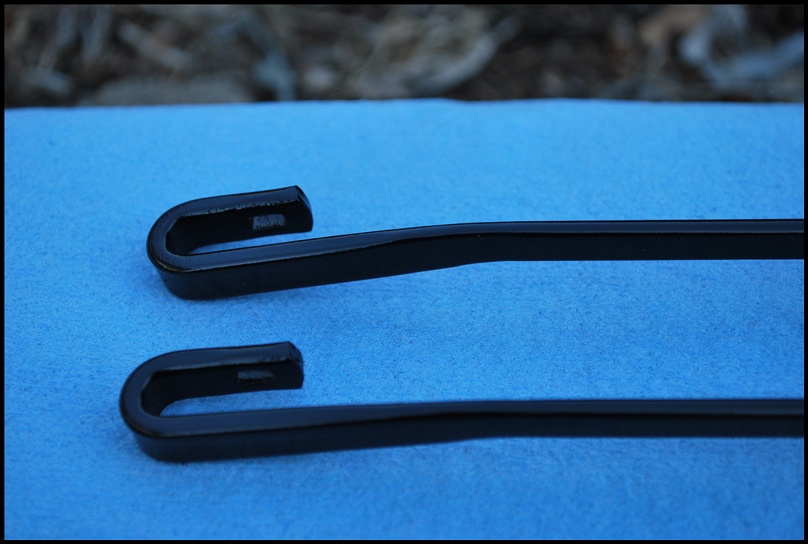
Bloody pins:
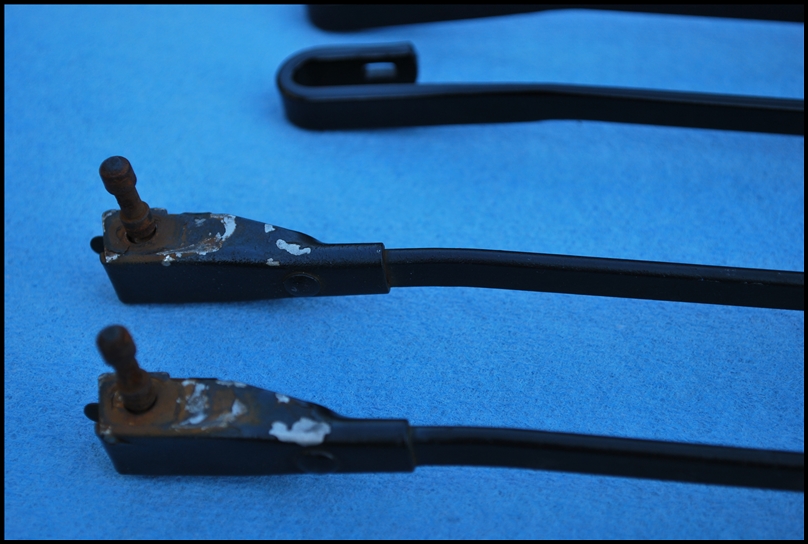
And the final product:
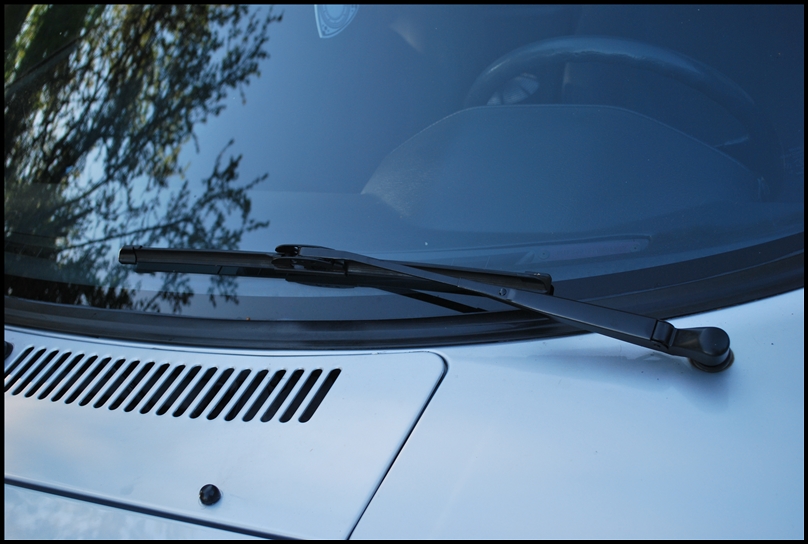


Trending Topics
#9
great job man only downside i see is that its too much work in my point of view, but props on the very clean install, might be something to look into later. . . i do need some wipers
#12
#18